1. Introduction: Why Crimping Hydraulic Hoses is Crucial
Crimping a hydraulic hose is a critical process in ensuring the proper hydraulic hose assembly. It involves securing the hose fittings onto the hose using a hydraulic hose crimping machine. This process creates hydraulic hose connections that can withstand high pressure without leaking, contributing significantly to the overall performance of the hydraulic system. Crimped hoses are essential for hydraulic hose leak prevention and for ensuring your system operates smoothly without failures or leaks. Understanding the hydraulic crimping process and using the correct crimping tool is essential for hydraulic hose installation.

1.1 What Is Hydraulic Hose Crimping?
Hydraulic hose crimping is the process of using a hydraulic hose crimping machine to compress the hose end fittings onto the hydraulic hose. This process ensures that the fittings are securely attached, creating a crimped hose that can handle high pressures typical in high-pressure hydraulic hose systems. Without proper crimping, hydraulic hose assemblies can fail, leading to catastrophic breakdowns.
1.2 Importance of Proper Crimping in Hydraulic Systems
Proper hose crimping tools and techniques ensure a secure and durable connection. Crimping hydraulic hoses for safety ensures the integrity of your hydraulic hose connections and prevents any leaks that could compromise the performance of the hydraulic system. A secure hose crimp not only increases the reliability of the system but also helps in hose pressure testing by maintaining the required pressure without failure.
1.3 Common Mistakes to Avoid While Crimping
When performing hydraulic hose repair or installation, avoid common mistakes such as using incompatible hydraulic hose fitting types or failing to use proper crimping pressure for hoses. Misalignment of the hose end fittings and poor fitting and hose alignment can lead to poor-quality crimps. These mistakes can result in hose crimping failure prevention challenges, leading to leaks and system failure.
2. Tools and Equipment Needed for Hydraulic Hose Crimping

2.1 The Essential Hose Crimping Machine
The hydraulic hose crimping machine is the cornerstone of any hydraulic hose crimping operation. It uses hydraulic force to apply a precise amount of pressure to compress the fitting onto the hose. Choosing the right hose crimping dies and machine settings is crucial to producing crimped hose quality that ensures the longevity and safety of the hydraulic system.
2.2 Choosing the Right Hose and Fittings
Selecting the correct hose fittings is vital for ensuring proper hose installation. Different types of hydraulic hose fitting compatibility must be considered, such as the material, size, and pressure rating. Using hose crimping tools that are compatible with these fittings ensures a tight, leak-proof connection, which is essential for hydraulic hose sealing methods.
2.3 Measuring Tools: Calipers and More
Accurate measurement of hydraulic hose size is critical before crimping. Tools like calipers or measuring tapes are used to measure both the hose and the fitting to ensure they match perfectly. This step ensures that the hose fits correctly into the crimping machine, avoiding any issues during the hydraulic hose crimping process.
2.4 Safety Gear to Keep You Protected
When working with high-pressure hydraulic systems, safety is a top priority. Always wear proper protective gear such as gloves, goggles, and safety clothing to prevent injury during hose crimping failure prevention or accidents. Hydraulic hose maintenance also requires careful handling of the hydraulic crimping machine to avoid any hazardous situations.
3. Understanding the Crimping Process: A Quick Overview
3.1 What Happens During the Crimping Process?
During the hydraulic hose crimping process, the hydraulic hose is inserted into the crimping machine, where it is compressed by the crimping dies. The machine applies pressure to the hose end fittings, creating a secure hose crimp that ensures a reliable hydraulic connection. The process must be precise to maintain the strength of the hose and ensure it doesn’t leak under pressure.
3.2 How Crimping Affects Hydraulic Hose Performance
The crimping process directly impacts the hydraulic hose performance. A properly crimped hose ensures that the fitting remains securely attached to the hose, preventing leaks and enhancing the system’s efficiency. Improper crimping can cause weak connections, leading to leaks and a drop in system pressure.
3.3 The Role of Crimping in Preventing Leaks and Failures
Hydraulic hose leak-proof connections are a must for ensuring that your hydraulic system operates at peak efficiency. Proper crimping ensures that fittings are securely attached to the hose, which is essential for hydraulic hose leak prevention. Pressure hose crimping allows the hose to withstand high pressure, preventing failures in critical components.
4. Step 1: Choosing the Right Hydraulic Hose and Fittings
4.1 Selecting the Correct Hose Size and Material
Choosing the correct hydraulic hose size and material is essential for creating a reliable hydraulic connection. Consider factors such as pressure ratings, fluid type, and environmental conditions when selecting the hose material. The correct hose and fitting combination ensure compatibility and a long-lasting, safe system.
4.2 Matching Fittings to Your Hose
Compatibility between the hose and the fittings is crucial to a secure connection. Hydraulic hose fitting types vary, so you must select the correct type based on the hose material and system requirements. Choosing the wrong fitting can cause leaks or failure in the system.
4.3 Understanding Pressure Ratings and Specifications
Understanding the pressure ratings and specifications of the hose and fitting is vital for hose crimping tips. Ensure that the hose and fitting are rated to handle the operating pressure of your system. Mismatched components can result in pressure loss, system failure, and unsafe operation.
5. Step 2: Measuring and Cutting the Hydraulic Hose
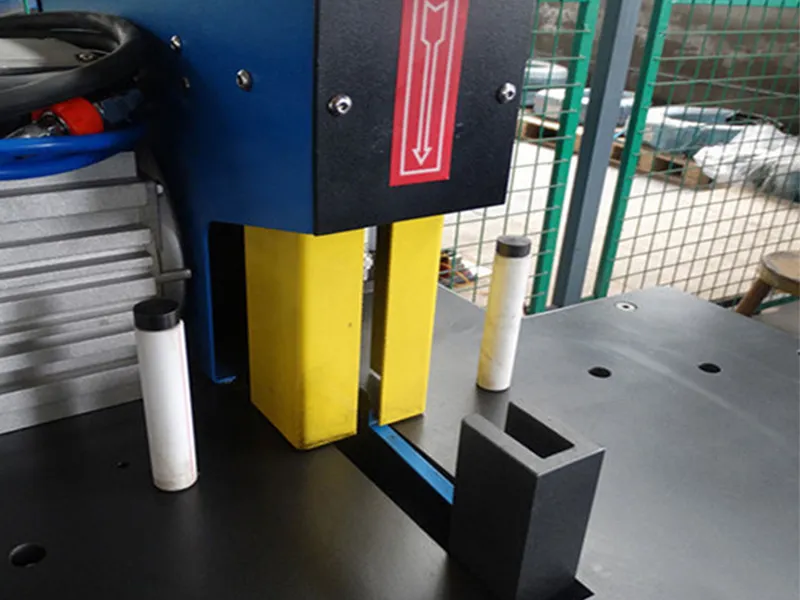
5.1 Importance of Accurate Hose Measurement
Accurate measurement is critical to ensure that your hose fits into the fittings and crimping machine. Use precise measuring tools like calipers to ensure that the hydraulic hose size is correct before cutting. This step is necessary to ensure that the final crimped hose fits properly and maintains the integrity of the hydraulic system.
5.2 Best Tools for Cutting Hydraulic Hoses
Cutting the hose cleanly is a vital part of the preparation process. Use hydraulic hose cutting tools such as rotary cutters or hose saws for a clean, even cut. This will ensure the hose fits properly into the crimping machine and the fittings align correctly.
5.3 Cutting Techniques for Clean and Even Cuts
To avoid fraying or damaging the hose during cutting, make sure to use a sharp blade and apply even pressure. Cutting the hose evenly ensures that the crimped hose will perform optimally without risk of leaks or other issues.
6. Step 3: Skiving the Hose (When Necessary)
6.1 What Is Skiving and Why It Matters
Skiving involves removing the outer layer of the hose to expose the inner reinforcement. This step is necessary for certain hoses to ensure a secure hose crimp. Skiving ensures that the fitting attaches securely to the inner hose material, resulting in a more reliable hydraulic hose connection.
6.2 Tools Needed for Skiving
To skive a hose correctly, use hose crimping tools that are designed for skiving. These tools help remove the outer layer without damaging the inner reinforcement, ensuring a clean and secure crimp.
6.3 Step-by-Step Skiving Process
Carefully remove the outer layer of the hose, ensuring that the inner reinforcement is left intact. This process requires precision to avoid cutting too deeply or unevenly, which can compromise the quality of the crimp.
6.4 When Skiving Is Not Required
Not all hoses require skiving. Some hoses have a thinner outer layer that doesn’t need to be removed. Check the manufacturer’s instructions to determine whether skiving is necessary for your specific hose.
7. Step 4: Inserting the Fitting into the Hose
7.1 How to Align and Insert the Fitting Properly
Proper fitting alignment is critical to ensuring that the crimp will be secure. Insert the hose end fittings into the hose, ensuring that they are aligned properly. Misalignment can result in an uneven crimp and weakened connections.
7.2 Common Problems When Inserting Fittings
One of the most common issues when inserting fittings is misalignment, which can lead to poor-quality crimps. If the fitting isn’t inserted straight, it can lead to leaks, reduced pressure tolerance, and hose failure.
7.3 Ensuring a Tight Fit
Once the fitting is aligned, ensure that it fits snugly into the hose. A tight fit is crucial for creating a secure hose crimp that will withstand pressure without leaks.
8. Step 5: Setting Up the Hose Crimping Machine
8.1 How to Prepare Your Crimping Machine
Before crimping, ensure that your hydraulic hose crimping machine is properly set up. Check the machine for any wear and tear, and
You have not enough Humanizer words left. Upgrade your Surfer plan.
8.2 Selecting the Right Die for the Job
Selecting the correct die is essential for creating a precise and secure crimp. The hose crimping dies should match the hydraulic hose size and the hydraulic hose fitting types being used. Using the right die ensures uniform pressure distribution, which results in a consistent crimp and a secure connection.
8.3 Adjusting the Pressure and Crimping Settings
Proper crimping pressure is key to producing a high-quality crimp. Too little pressure can result in a loose connection, while too much pressure can damage the hose or fittings. Adjust the crimping pressure for hoses according to the manufacturer’s guidelines and check that the settings on the hydraulic hose crimping machine are correctly calibrated.
9. Step 6: Calibrating the Crimping Machine
9.1 Why Calibration Is Crucial for a Secure Crimp
Calibration ensures that the machine applies the correct amount of force, creating a consistent and secure hydraulic hose crimping process. Proper calibration is essential for maintaining the integrity of the hose connection and preventing potential failures during operation.
9.2 How to Properly Calibrate Your Crimping Machine
To calibrate the machine, use a sample hose and fitting to test the settings. Make adjustments to the crimping pressure and die alignment until the crimp is uniform and meets the necessary standards. Regular calibration ensures that your crimping machine calibration remains accurate over time.
9.3 Testing Calibration with a Sample Crimp
Once the crimping machine is calibrated, perform a test crimp on a sample hose. Inspect the crimp for uniformity and consistency. Use measuring tools like calipers to check the crimp’s dimensions and ensure they meet the specified requirements.
10. Step 7: Crimping the Hydraulic Hose
10.1 Inserting the Hose and Fitting into the Crimper
Insert the hose and fitting into the hydraulic hose crimping machine, ensuring that the hose is properly positioned within the dies. The fitting should be inserted securely into the crimping tool, aligning it with the center of the die. This ensures a uniform and secure hose crimping process.
10.2 Activating the Crimping Process
Activate the hydraulic crimping machine to apply pressure. As the machine compresses the fitting onto the hose, monitor the process to ensure the crimp is uniform and consistent. The pressure hose crimping should be done carefully to avoid damaging the hose or fitting.
10.3 Monitoring the Crimp to Ensure It’s Perfect
Throughout the crimping process, check for any signs of irregularities. The crimp should be tight and evenly distributed around the fitting. A proper crimp ensures the hose is securely attached to the fitting and will perform well under high pressure.
11. Step 8: Inspecting the Crimp for Quality
11.1 What to Look for in a Proper Crimp
A well-crimped hose should show no gaps or irregularities around the fitting. The crimped area should be smooth, with no visible defects such as cracks or deformations. The hydraulic hose leak-proof connections will be tight and secure, with no visible signs of damage.
11.2 Using Measuring Tools to Check Crimp Dimensions
To confirm the crimp’s quality, use measuring tools like calipers to check the crimped area’s diameter. It should match the size specified for the hose and fitting. Hose pressure testing can also be performed to ensure that the crimp can withstand the required pressure.
11.3 Performing a Visual Inspection for Leaks
Visually inspect the crimp for signs of leaks. You can perform a simple pressure test to verify that the crimped hose does not leak under the working pressure. This is essential to ensure the safety and efficiency of the hydraulic system.
12. Common Problems and Troubleshooting Tips
12.1 Misalignment Issues and How to Fix Them
Misalignment of the hose or fitting is a common problem in the crimping process. This can result in an uneven crimp or weak connection. If you notice misalignment, reposition the fitting and hose carefully before starting the crimping process again.
12.2 How to Handle Over-Crimping or Under-Crimping
Over-crimping can damage the hose or fitting, while under-crimping can result in a loose connection. Always ensure that you apply the correct amount of pressure. Adjust the crimping machine calibration and crimping pressure for hoses to avoid these issues.
12.3 Dealing with Crimping Machine Malfunctions
If the hydraulic hose crimping machine malfunctions during the crimping process, stop immediately. Inspect the machine for issues such as misaligned dies, worn-out components, or incorrect settings. Regular machine maintenance can help prevent malfunctions.
13. The Best Practices for Crimping Hydraulic Hoses
13.1 Ensuring Consistency with Each Crimp
To maintain a consistent crimp quality, follow the same process every time. Use the correct hose crimping dies and ensure the machine settings are always calibrated. This consistency will improve the reliability and performance of your hydraulic hose installations.
13.2 Avoiding Contamination During the Process
Contamination of the hose or fittings during the crimping process can lead to poor-quality crimps. Always keep your workspace clean and ensure that your hydraulic hose cutting tools are free from debris.
13.3 Regular Maintenance of Your Crimping Equipment
Regularly check and maintain your crimping machine, tools, and dies to ensure they remain in top condition. Well-maintained equipment reduces the risk of faulty crimps and improves the efficiency of the crimping process.
14. Safety Tips and Precautions
14.1 Importance of Wearing Protective Gear
Always wear protective gear, such as gloves, safety goggles, and clothing, when performing hydraulic hose installation or crimping. These safety precautions help protect against potential accidents during the hydraulic hose crimping process.
14.2 How to Safely Handle the Crimping Machine
Handling the hydraulic hose crimping machine requires care. Always follow the manufacturer’s instructions and ensure the machine is securely positioned before use. Never stand directly in front of the machine while it’s operating to avoid injuries in case of unexpected hose bursts.
14.3 Dealing with High-Pressure Hoses Safely
High-pressure hydraulic hoses require special care. Always ensure that the hydraulic hose fitting compatibility is correct and that the crimped hose is tested for pressure before use. This will help prevent accidents caused by pressure-related failures.
15. How to Test Your Crimped Hose Assembly
15.1 Visual Inspection Techniques
Before using a crimped hose, perform a thorough visual inspection. Look for any signs of deformation, cracks, or misalignments around the crimped area. This will help detect any issues early and prevent future failures.
15.2 Pressure Testing Your Crimped Hose
Conduct hose pressure testing to ensure the crimp can handle the required pressure. This is a critical step in confirming that your crimped hose can function safely in its intended application.
15.3 Common Testing Methods for Hose Durability
In addition to pressure testing, you can test the crimped hose for flexibility and longevity. Consider using hydraulic fluid to check for any leakage or weakness in the connection. This helps ensure the durability and safety of the hose under operational conditions.
16. Maintaining Your Hydraulic Hose and Fittings
16.1 Cleaning and Storing Hydraulic Hoses Properly
Proper storage and maintenance of hydraulic hoses are essential to ensuring their longevity. Clean the hoses regularly and store them in a dry, cool place away from direct sunlight. This helps prevent damage and degradation over time.
16.2 How to Extend the Lifespan of Crimped Hoses
To extend the lifespan of crimped hoses, perform regular inspections and maintenance. Replace any worn-out hose end fittings or damaged hoses immediately. This proactive approach helps maintain the integrity of the system.
16.3 When to Replace Crimped Hoses
Knowing when to replace crimped hoses is crucial for maintaining the safety and efficiency of your hydraulic system. Replace any hoses that show signs of wear, leaks, or poor performance to prevent potential system failures.
17. Frequently Asked Questions (FAQ) About Hydraulic Hose Crimping
17.1 How Do I Know If My Crimp Is Properly Done?
A properly done crimp will be tight and uniform, with no visible defects. Use measuring tools like calipers to check the dimensions of the crimp and ensure it meets the specifications.
17.2 Can I Reuse Fittings or Crimped Hoses?
Reusing fittings or crimped hoses is generally not recommended, as they may not maintain the required pressure and security. Always replace them with new components to ensure safe operation.
17.3 What Are the Signs That a Crimped Hose Needs to Be Replaced?
Signs that a crimped hose needs replacement include visible damage, cracks, leaks