1. Introduction: The Importance of Properly Crimped Hose Fittings
When it comes to hydraulic systems, every connection matters. The difference between smooth operation and catastrophic failure often lies in the details—especially in the hose crimper. Hydraulic hose crimping is the vital process that ensures hoses and hydraulic hose fittings stay secure under pressure. A well-crimped hose fitting guarantees seamless fluid flow, prevents dangerous leaks, and ensures equipment runs efficiently. However, improperly done hose crimping can lead to downtime, costly repairs, and safety hazards. Whether it’s in heavy machinery, industrial equipment, or everyday applications like hydraulic office chairs, crimped hose fittings play a crucial role in ensuring everything runs smoothly. But what exactly is crimping, why does it matter so much, and how can you make sure you’re doing it correctly? In this post, we’ll break down the essentials of hose fitting crimping, explore its significance for system performance, and provide insights into where and how crimping plays a crucial role in real-world applications.
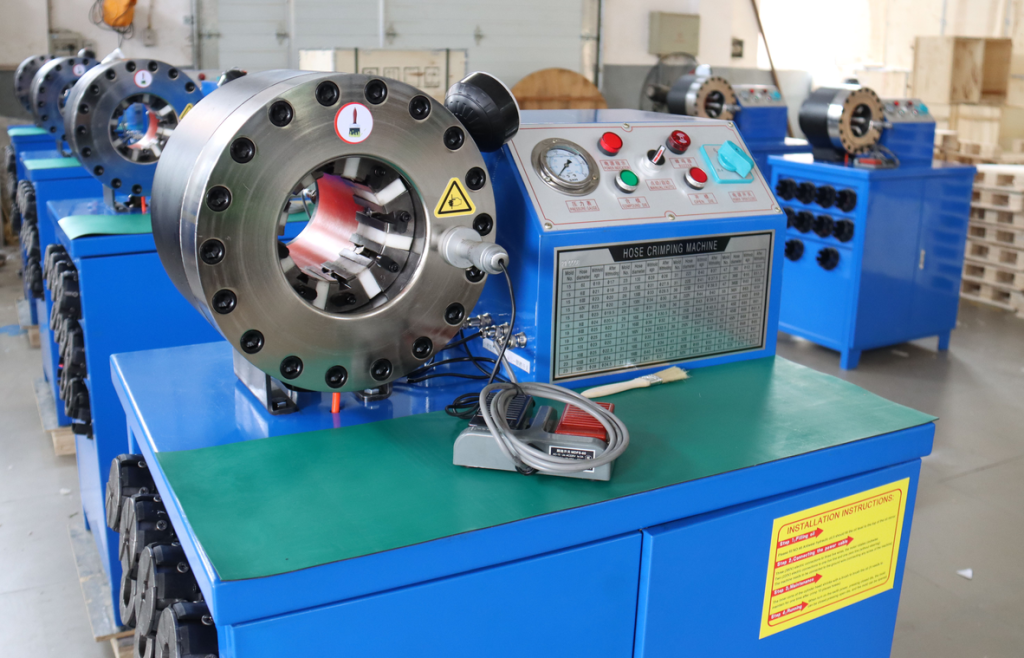
What Crimping Is and Why It Matters
Crimping tools compress a hydraulic hose fitting onto the end of a hose, forming a permanent, leak-proof seal. While this may seem like a simple task, it’s essential for ensuring the system can handle high-pressure and temperature variations. Without proper hose crimping, leaks, failures, or even catastrophic breakdowns are inevitable. The hose crimper tool ensures that the connection between the hose and fitting is secure and will perform under demanding conditions.
How Crimping Affects Hydraulic System Performance
Proper hydraulic crimping ensures that the hydraulic system performs at its peak. When crimped hose fittings are installed correctly, the system experiences smooth fluid flow, stable hydraulic hose pressure, and reduced risk of failure. In contrast, improper hose crimping can result in low pressure, erratic fluid flow, and even dangerous leaks. Whether you’re dealing with a manual hose crimper or a hose crimping machine, it’s essential to achieve the right crimp diameter and crimping force to guarantee the system’s performance.
Common Applications of Crimped Hose Fittings
Crimped hose fittings are used in a wide range of industries and applications, from heavy-duty machinery and industrial systems to office furniture with hydraulic lifts. Every time a hose assembly is in place, whether in construction or automotive industries, hydraulic hose crimping ensures that the connection stays strong under pressure. Crimping for industrial machines and high-pressure hose crimping are just a few examples where hose crimping is essential for reliable and safe operation.
2. Understanding Hose Fittings and Crimping Basics
Before diving into the technicalities of crimping, it’s important to understand the basics of hose fittings and their role in the crimping process. Different types of hydraulic hose fittings are used for specific applications, and selecting the right one is crucial for achieving the best crimp.
Types of Hose Fittings and Their Applications
There are various types of hose fittings, such as threaded, push-on, and flanged fittings, each designed for specific tasks. Some fittings are more suitable for high-pressure systems, while others are ideal for heavy-duty applications. Hose fitting installation can vary depending on the fitting type and its application. It’s important to choose the correct hose fitting based on factors like pressure ratings and compatibility with the hose.
Essential Crimping Terminology and Materials
To effectively use a hose crimping machine, it’s essential to understand the key terminology and materials involved in the crimping process. Crimping die, crimping force, and crimping precision are just some of the factors that impact the quality of a crimp. The materials used for hydraulic hose systems, like stainless steel or brass, will also influence the crimping method and pressure applied.
Key Components for Successful Crimping
A successful crimp relies on several key components: the hose, the hydraulic hose fitting, and the crimping equipment. These elements must work together to create a strong, leak-proof seal. Ensuring compatibility between the hose and fitting, as well as using the appropriate crimping tools for high-pressure hoses, is crucial for achieving reliable results.
3. Tools You Need for Crimping Hose Fittings
The right tools make all the difference when it comes to hose crimping. Whether you are using a manual hose crimper, an automatic hose crimper, or a hose crimping machine, each tool is designed to meet specific needs and ensure quality results.
Hydraulic vs. Manual Crimping Tools
Hydraulic crimping machines are ideal for large-scale operations and provide consistent, high-quality crimps. For smaller jobs, a manual hose crimper or portable hose crimper may be sufficient. Understanding the difference between manual and automatic hose crimper options will help you select the best tool for your needs. Each tool offers unique benefits depending on the scale and demands of your project.
Choosing the Right Equipment for Your Job
To achieve high-quality results, selecting the right crimping tool set is essential. Whether you’re performing hydraulic hose cutting and crimping or simply installing a hose fitting, using the right tool ensures that the crimping process is done accurately and efficiently. Ensure that the crimping machine setup is calibrated properly to apply the correct crimping pressure and crimping force for the best results.
Maintaining Your Crimping Tools
Regular crimping tool maintenance is essential to ensure optimal performance. Over time, the crimping die and other parts of your tools may wear out. Performing regular crimping tool calibration and inspecting your tools for wear will help you avoid issues and maintain consistent crimping performance.
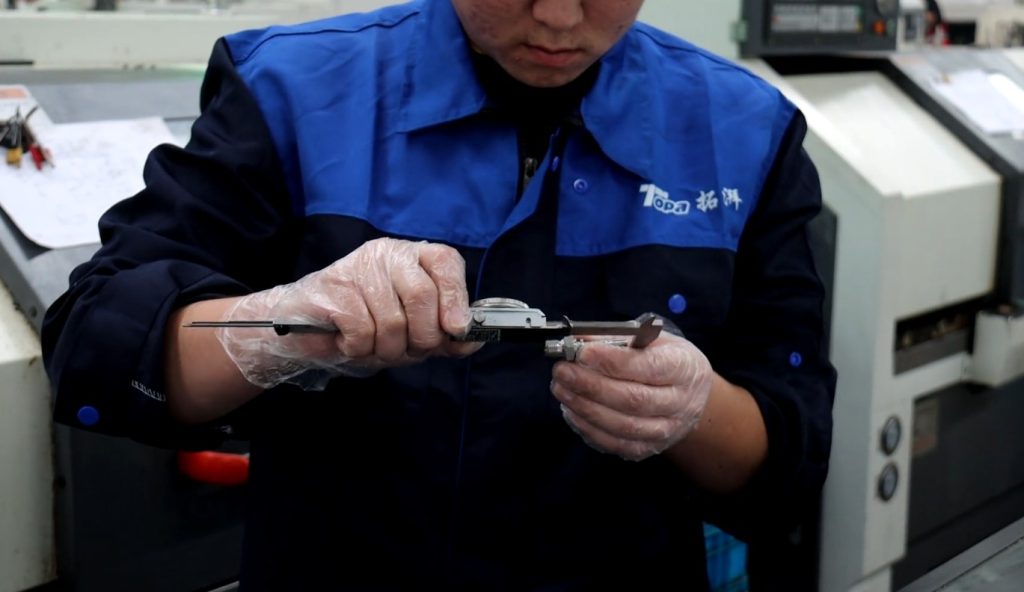
4. Step-by-Step Guide to Crimping Hose Fittings
The hose crimping process involves several steps to ensure a perfect crimp every time. By following these steps, you can achieve a secure and leak-proof hose fitting.
Measuring, Cutting, and Preparing Hose and Fittings
Accurately measure and cut the hose to the correct length before inserting the hydraulic hose fitting. Clean both the hose and fitting to remove any debris or contaminants. A precise cut and clean fitting ensure the best hose and fitting compatibility, reducing the risk of issues during hose fitting installation.
Crimping Process: Inserting, Positioning, and Applying Pressure
Insert the fitting into the hose and align it properly in the hose crimping machine. Apply the correct crimping pressure to compress the fitting securely around the hose. The crimp diameter and the crimping force adjustment will depend on the type of hose, fitting, and application. Consistent crimping precision is key to ensuring a leak-proof connection.
Inspecting the Crimp for Quality and Consistency
After crimping, it’s important to inspect the crimped hose fittings to ensure the hose fitting seal is secure. Use a crimping tool set to check for any imperfections in the crimped connection. A proper inspection helps prevent issues that could lead to leaks or failures in the system.
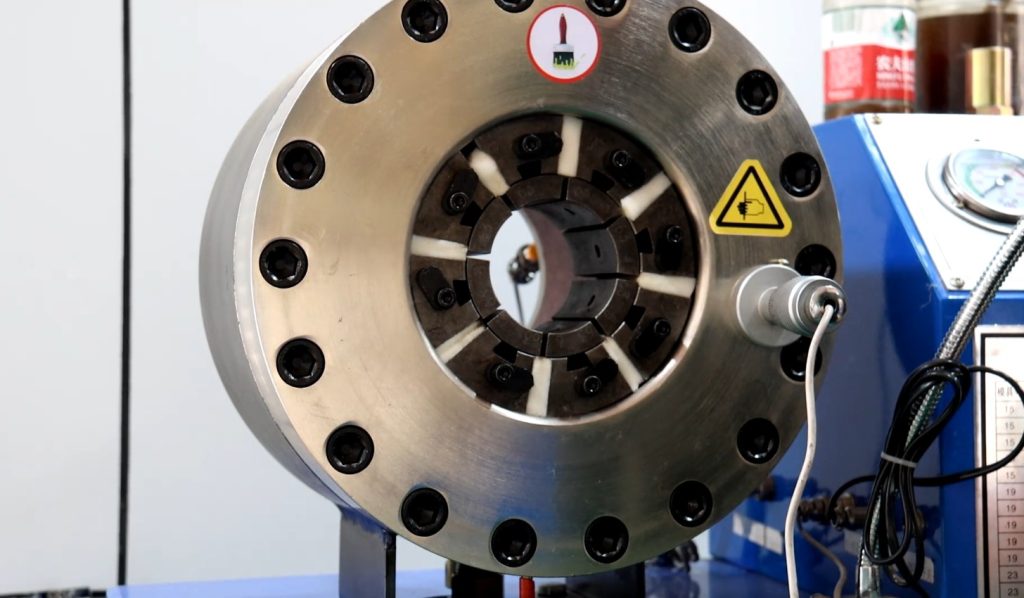
5. Common Crimping Mistakes and How to Avoid Them
Even experienced technicians can make mistakes during the crimping procedure. Knowing what to avoid can help ensure that your crimps are done correctly.
Over-Crimping vs. Under-Crimping
Over-crimping can damage the hose or fitting, while under-crimping results in a weak connection that is prone to leaks. Ensuring the right balance of crimping pressure and crimping force is crucial to achieving a high-quality crimp.
Misalignment and Tool Wear
Improper alignment of the hose or fitting in the crimping machine can lead to uneven crimps, which may cause issues later on. Regular crimping tool maintenance and tool calibration can help prevent misalignment and ensure precise results.
Troubleshooting Inconsistent Crimps
If you’re noticing inconsistent crimps, it may be time to troubleshoot. Common causes include incorrect crimping pressure, tool wear, or improper hose fitting installation. Ensure that your hydraulic crimping process is running smoothly and that your tools are in optimal condition.
6. Crimping Standards and Specifications
Adhering to the correct hose crimping standards is essential for ensuring that the crimped hose fittings are safe and reliable.
Understanding Industry Standards for Crimping
Industry standards like those set by SAE and ISO provide guidelines for the crimping fitting certification and crimping machine calibration. Following these standards ensures that your crimps meet safety and performance requirements, minimizing the risk of failure.
How to Read Crimping Specifications and Certifications
Understanding crimp diameter specifications, crimping pressure, and hydraulic hose pressure is key to achieving high-quality crimping. Always verify that your hose and fitting compatibility meets the necessary standards before starting the crimping process.
Ensuring Compliance with Safety and Quality Regulations
Crimping fitting certification ensures that the hose assembly will perform reliably under pressure. Always check that your crimped fittings meet the required safety standards and that your crimping tools are properly maintained for maximum efficiency.
7. Testing Crimped Hose Fittings for Quality Assurance
Once crimping is complete, testing the finished assembly is crucial for ensuring the integrity of the connection.
Pressure Testing and Visual Inspections
Pressure testing hose fittings is one of the most effective ways to ensure that the crimp is secure. A visual inspection can also help detect any imperfections in the crimped connection that might lead to leaks or failures.
Identifying Leaks and Weak Seals
During the testing phase, check for any signs of leaks around the crimp. Ensuring a proper hose fitting seal is essential for a leak-free operation. If leaks are detected, inspect the hose crimping process to identify areas that need improvement.
Common Crimping Problems and Detection Methods
Common issues with crimped hose fittings include misalignment, improper crimp diameter, or insufficient pressure. Identifying these issues early through testing will help you prevent failures and ensure the longevity of your hydraulic system.
8. Cost-Saving Tips for Crimping Hose Fittings
Efficient crimping not only ensures safety and reliability but can also save you money in the long run.
Reducing Material Waste and Maximizing Efficiency
Proper hydraulic hose cutting and crimping can reduce material waste by ensuring that only the necessary amount of hose and fittings are used. By selecting the correct crimping equipment for the job, you can maximize efficiency and minimize wasted resources.
Investing in Quality Crimping Tools for Long-Term Savings
Investing in high-quality crimping tools for hydraulic hoses ensures long-term savings by delivering consistent, reliable crimps. A well-maintained crimping tool set will reduce the need for frequent replacements and repairs.
Streamlining Your Crimping Process
Streamlining the hose assembly procedure and crimping machine setup can help reduce labor costs and improve overall efficiency. By organizing your workspace and following a systematic approach, you can cut down on production time and improve output.
9. Conclusion: Perfecting Your Crimping Technique
Mastering the hose crimping process is essential for ensuring the safety, reliability, and longevity of your hydraulic systems. With the right crimping tools, hydraulic crimping techniques, and adherence to industry standards, you can guarantee that your crimped hose fittings will perform efficiently and securely under pressure. Proper crimping precision, tool maintenance, and calibration are critical to achieving the best results every time. With the right knowledge and tools, you can ensure the integrity of your hydraulic systems and prevent costly failures.