1. Introduction
Hydraulic systems power everything from heavy machinery to industrial equipment, and at the heart of these systems are hydraulic hoses. These hoses are the unsung heroes, delivering high-pressure fluids that keep operations running smoothly. But what happens when these hoses start to fail? That’s where hydraulic hose crimping comes in. The process of crimping hydraulic hoses is more than just a technical step—it’s a critical part of maintaining hydraulic hose assembly integrity, ensuring that the connection between the hose and hydraulic fittings can withstand extreme pressures and harsh environments. Done incorrectly, however, it could lead to a hydraulic hose failure. By using the right crimping tools and following the correct hose crimping techniques, you can ensure long-lasting, leak-free connections. In this guide, we’ll explore what crimping hydraulic hoses is, why it’s vital for the longevity of your hydraulic hoses, and how doing it right can save you from costly downtime.
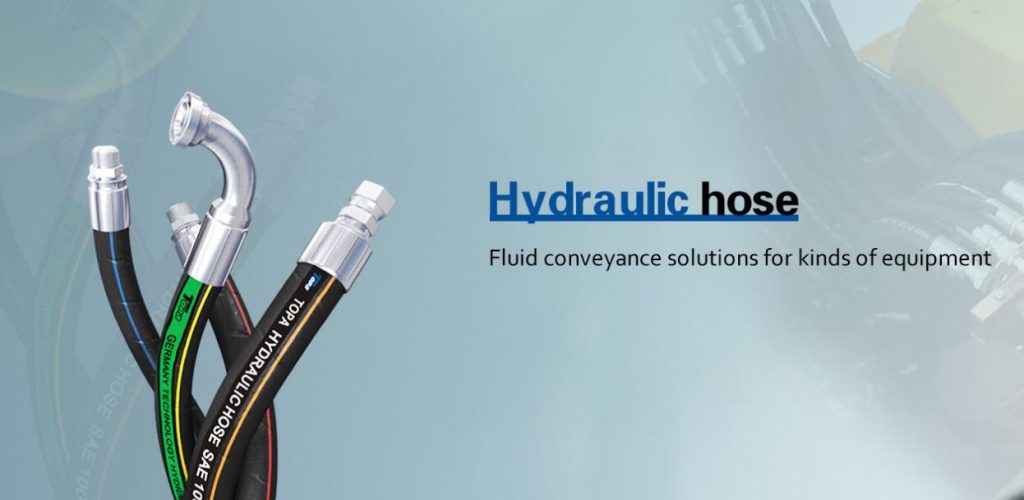
1.1 What Is Hydraulic Hose Crimping and Why Is It Important for Hydraulic Hoses?
At its core, hydraulic hose crimping involves securing a hydraulic hose fitting onto the end of a hydraulic hose using a crimping machine. This process compresses the fitting to create a tight, leak-proof seal, ensuring that high-pressure fluids flow efficiently without risk of leakage or rupture. While this might sound simple, the science behind it is complex. A poor crimp job can compromise the entire hydraulic system, leading to breakdowns, inefficiencies, and costly repairs. Hydraulic hose inspection and hose and fitting connection checks are critical to ensure the right fit. Understanding the importance of hydraulic crimping can help you avoid these issues and prolong the life of your hydraulic systems.
1.2 Common Hydraulic Hose Failures and How Crimping Helps Prevent Them
Hydraulic hose failures are often a result of improper hydraulic hose fitting installation or incorrect crimping. Without the right amount of pressure or alignment during crimping, the hose and fitting connection may fail, leading to leaks or bursts under pressure. These failures can cause significant disruptions, especially in industries relying on constant machine performance. By mastering the crimping process and using the right crimping tools, you can ensure your hoses stay in optimal working condition, reducing the risk of these common failures and maintaining the efficiency of your operations.
2. Understanding Hydraulic Hose Components
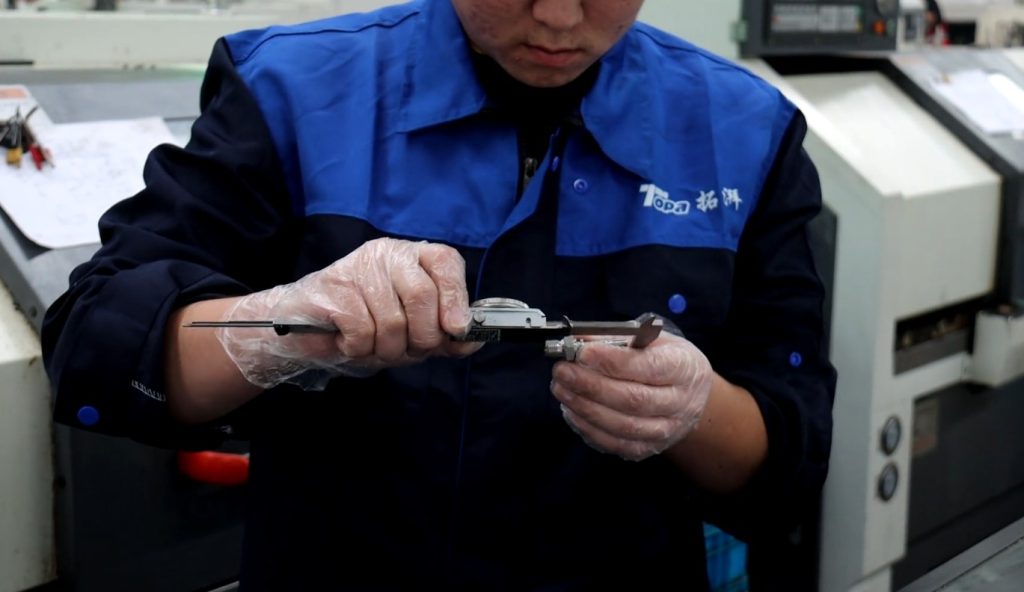
Before diving into the crimping process, it’s essential to understand the components that make up a hydraulic hose assembly. Each part plays a vital role in ensuring that your system operates efficiently and safely. The hydraulic hose, the hydraulic fittings, and the crimping collars all work together to form a durable and leak-free connection. In this section, we’ll break down each component so you can understand how they contribute to the crimping process and why choosing the right materials is crucial.
2.1 The Hydraulic Hose: Types and Materials
The hydraulic hose is the flexible conduit that carries hydraulic fluid through a system. Typically made from rubber or synthetic materials, the hose is reinforced with steel braids or spirals for strength and flexibility. Different types of hoses are designed to withstand various pressures and temperatures, and selecting the right hose for your hydraulic hose assembly is crucial to achieving a secure and effective crimping. Understanding the pressure rating, fluid compatibility, and temperature range of your hydraulic hoses is key to ensuring the crimping process is performed correctly.
2.2 The Hydraulic Fittings: Different Types and Their Purpose
Hydraulic fittings are the connectors that join hoses to pumps, valves, and other parts of the system. These fittings come in various shapes and sizes, such as male, female, elbow, or straight connectors. Proper hydraulic fitting installation is essential to prevent leaks and ensure the durability of the entire hydraulic system. Using the wrong fitting or one that is incompatible with the hose can lead to issues down the line, including hydraulic fluid leakage and premature failure.
2.3 The Crimping Collars: What They Do and Why They’re Critical
The crimping collar (also known as a ferrule) is the metal sleeve that compresses the hydraulic hose fitting and hose together. It creates the tight seal required to ensure no fluid leaks from the connection. Proper ferrule crimping is essential, as a misaligned or incorrectly sized collar can result in an unreliable connection. Ensuring that the crimping collars are correctly selected and fitted will prevent problems like hose leak prevention and ensure optimal hose pressure resistance.
3. Crimping Tools and Equipment
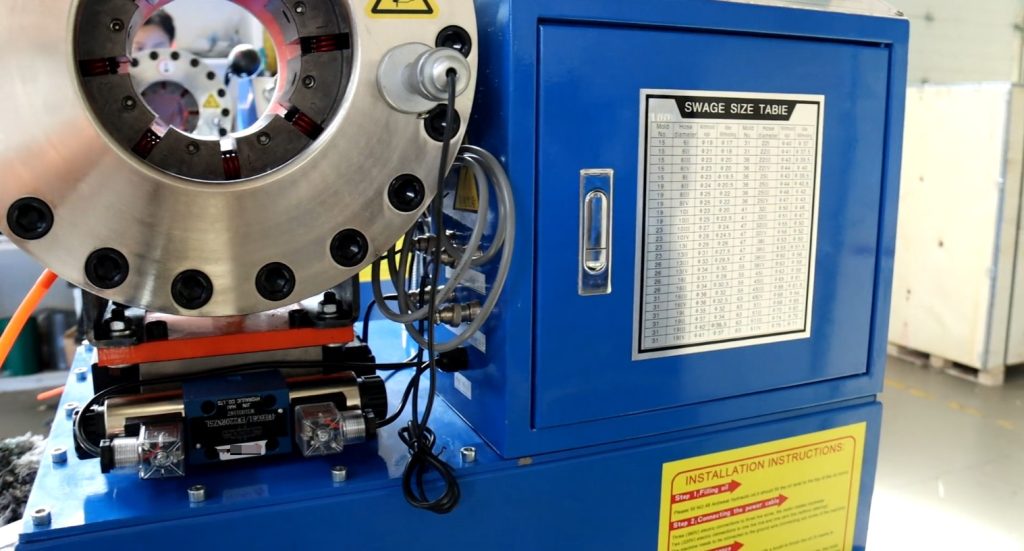
When it comes to crimping hydraulic hoses, the tools you use make all the difference. Selecting the appropriate hose crimping tools will ensure the right amount of pressure is applied and that the crimp is performed evenly and securely. There are several tools available for hydraulic crimping, and in this section, we’ll explore the options so you can choose the best one for your needs.
3.1 Manual Crimping Tools: Pros and Cons
Manual crimping tools are ideal for small-scale operations or mobile services. These tools are affordable and relatively easy to use. However, they require more effort from the operator and may lack the precision needed for high-pressure applications. Hydraulic hose repair using manual tools can be effective for basic tasks but may not provide the consistency required for industrial hose crimping.
3.2 Hydraulic Crimping Machines: Features to Look For
Hydraulic crimping machines offer more precision and power than manual tools, making them suitable for high-volume production. These machines are ideal for industrial hose crimping and custom hydraulic hoses that require consistent and high-quality crimps. When selecting a crimping machine, be sure to choose one with adjustable pressure, the appropriate crimping die sizes, and user-friendly features. This ensures your machine is versatile enough to handle various hose sizes and pressure requirements.
3.3 Choosing the Right Crimping Tool Selection
The right crimping tool selection is critical to achieving consistent results in the crimping process. Depending on the scale of your operation, you may opt for a manual tool or a hose crimping machine. However, it’s essential to match the tool with the specific requirements of the hose and fitting, including material compatibility, pressure rating, and the complexity of the hose installation procedures.
4. Step-by-Step Guide to Crimping Hydraulic Hose
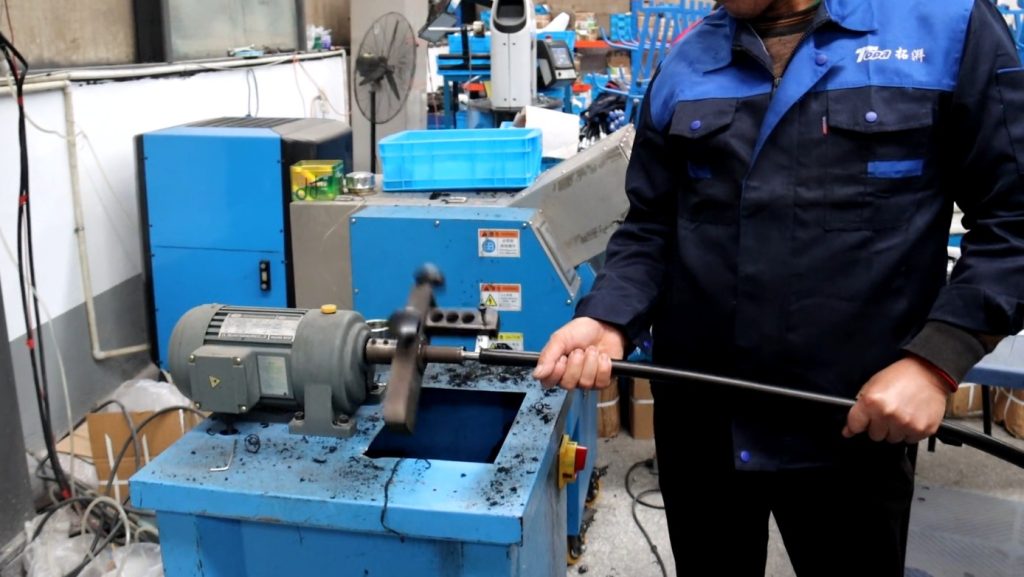
Now that we’ve covered the basics of hydraulic hose crimping, it’s time to dive into the step-by-step process. This guide will walk you through everything from preparing the hose to inspecting the finished crimp to ensure your hydraulic hose assembly is leak-free and durable.
4.1 Step 1: Preparing the Hydraulic Hose and Fittings
Start by cutting the hydraulic hose to the required length. Be sure to use a sharp cutter to avoid fraying the hose’s edges, which could interfere with the crimping process. After cutting, inspect the hydraulic fittings and the hose for any debris or damage. A clean, smooth fitting and hose are essential for creating a strong hose and fitting connection.
4.2 Step 2: Selecting the Correct Crimping Die
The next step is selecting the correct crimping die for your hydraulic hose assembly. Dies come in various sizes to fit different hoses and fittings, and choosing the right one ensures a proper seal. Using the wrong die can lead to hydraulic hose failure or leaks. Ensure the crimping die matches the hose’s diameter and the fitting’s specifications.
4.3 Step 3: Inserting the Hydraulic Fitting into the Hydraulic Hose
After selecting the appropriate crimping die, insert the hydraulic fitting into the hose. Ensure that the hose is fully inserted into the fitting and that the fitting’s collar is aligned with the hose end. Any misalignment can weaken the hose and fitting connection, potentially leading to leaks or bursts under pressure.
4.4 Step 4: Positioning the Hose in the Crimping Machine
Place the hose assembly into the crimping machine, ensuring the hydraulic fitting is properly aligned with the crimping die. Incorrect alignment can result in uneven pressure distribution, which can affect the quality of the crimp. Ensure that the fitting is in the correct position before applying pressure.
4.5 Step 5: Crimping the Hose: Pressure and Time Considerations
Now it’s time to apply pressure. Use the crimping machine to compress the fitting onto the hose. Ensure the machine is set to the appropriate pressure for the hose and fitting combination. Too much pressure can distort the fitting, while too little pressure can result in a weak crimp that may fail. Refer to the manufacturer’s guidelines for crimp pressure calibration and the recommended crimping die sizes.
4.6 Step 6: Inspecting the Crimped Hose: Key Indicators of Quality
Once the crimp is complete, carefully inspect the hose assembly. Look for smooth, uniform compression around the hydraulic fitting and check for any gaps or deformation. A properly crimped hose should show no visible signs of over-crimping or under-crimping. Regular hydraulic hose inspection is key to ensuring the crimping process was successful.
5. Factors That Affect the Crimping Process
Several factors can influence the quality of your crimp. Understanding these factors is key to ensuring a secure, durable connection. Let’s explore some of the most important variables to consider during the hydraulic crimping process.
5.1 Hydraulic Hose Size and Pressure Rating
Different hoses are designed to withstand different pressure ratings. When selecting your hydraulic hose, make sure to match it to the application’s pressure requirements. Using a hose that is too small for high-pressure applications can lead to failure, while using an oversized hose may make crimping more difficult.
5.2 Temperature and Environmental Conditions
Environmental factors like temperature and humidity can also affect the crimping process. Hydraulic hoses may become brittle in extreme cold or softer in high heat, both of which can affect crimp quality. Ensure you account for these conditions when selecting hydraulic hoses and crimping collars.
5.3 Material Compatibility: Hydraulic Fittings and Hose Types
Not all materials are compatible with one another. Ensure that the hydraulic fittings and the hydraulic hose are made from materials that work well together to prevent issues such as hydraulic fluid leakage or premature wear. The right combination of materials ensures a long-lasting, reliable crimp.
6. Troubleshooting Common Crimping Problems
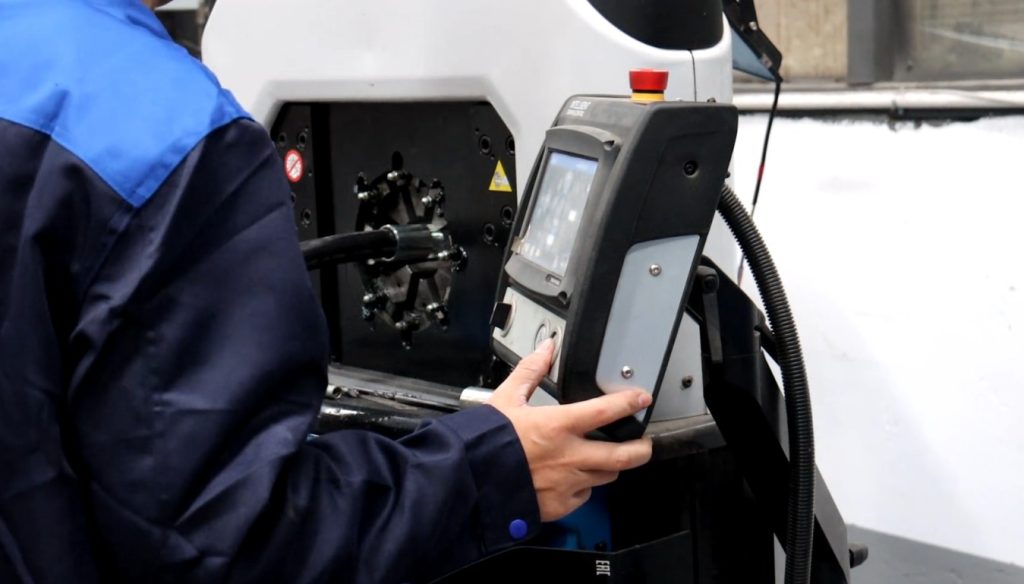
Even with the best tools and materials, crimping hydraulic hoses can sometimes present challenges. Identifying and addressing these issues early will save you time, money, and prevent potential failures in your hydraulic systems. Let’s look at some of the most common crimping problems and how to troubleshoot them effectively.
6.1 Over-Crimping and Under-Crimping: What Happens and How to Avoid It
Over-crimping occurs when too much pressure is applied, causing the fitting or hose to deform. On the other hand, under-crimping results in a loose or weak connection that may fail under pressure. Both issues can be avoided by using the right amount of pressure with the proper crimping tool selection. Always check the manufacturer’s guidelines for the correct crimp pressure calibration and ensure that you use the correct crimping die sizes for the hose and fitting being used.
6.2 Misalignment of Fittings and How It Affects Hose Performance
Misalignment during the crimping process can cause uneven pressure distribution, which weakens the connection. This misalignment can lead to leaks and decreased hose performance. Be sure to carefully align the hydraulic fittings with the hydraulic hose and the crimping die before applying pressure. Proper alignment ensures a uniform and secure connection.
6.3 Why Crimping Dies Wear Out and How to Extend Their Lifespan
Crimping dies wear out over time due to constant use and high pressure. Worn dies can lead to inconsistent crimps, which may cause leaks or hose failures. To extend the lifespan of your dies, make sure to regularly inspect them for signs of wear and replace them when necessary. Proper cleaning and maintenance of hose crimping tools are also essential to ensure the dies perform optimally.
7. Safety Precautions When Crimping Hydraulic Hoses
Working with high-pressure fluids and powerful crimping tools requires adherence to strict safety protocols. Taking the right precautions will help you avoid accidents and ensure your hydraulic hose assembly is secure and safe for operation.
7.1 Personal Protective Equipment (PPE) for Crimping
Always wear the appropriate personal protective equipment (PPE) when crimping hydraulic hoses. This includes safety goggles to protect your eyes from flying debris, gloves to protect your hands, and steel-toed boots to prevent injuries from falling tools or equipment. Safety is paramount to avoid accidents during the hydraulic hose crimping process.
7.2 Handling Hydraulic Fittings Safely
Hydraulic fittings can be heavy, sharp, and potentially hazardous if not handled with care. Always store hydraulic fittings in a secure, organized manner, and handle them gently to avoid injury. Ensuring that the hydraulic hose fitting is free from defects and clean will help prevent any issues during the hydraulic hose inspection process.
7.3 Avoiding Injuries During Crimping and Testing
When testing crimped hydraulic hoses, always use a secure test bench and stand clear of the hose to avoid injury in the event of a failure. Proper testing techniques, such as pressure testing hydraulic hoses, ensure that each hose assembly is safe for operation. Always verify that your hose crimping tools are properly calibrated and well-maintained to avoid malfunctions during use.
8. Testing the Crimped Hydraulic Hose
Once you’ve completed the crimping process, it’s essential to test the hydraulic hose assembly to ensure the crimp is secure and reliable. In this section, we’ll cover the best practices for pressure testing hydraulic hoses and inspecting the crimped hose for quality assurance.
8.1 Pressure Testing: How to Do It Right
Pressure testing hydraulic hoses is a critical step in verifying the quality and reliability of a crimped hydraulic hose. To properly test, apply the correct pressure according to the hose’s specifications and monitor for any signs of leakage or failure. Following industry standards and the SAE standards for hydraulic hoses is essential to ensure the testing process is both safe and accurate.
8.2 Visual Inspection: What to Look For After Crimping
A visual inspection is one of the most effective ways to verify the quality of a crimped hydraulic hose. Look for uniform compression around the hydraulic fitting, ensuring that there are no visible gaps, cracks, or over-crimping marks. A properly crimped hose will have a smooth, even compression that ensures a secure, leak-proof connection.
8.3 The Importance of Documenting Tests for Quality Control
Documenting pressure testing and the results of your hydraulic hose inspection is essential for maintaining quality control. This ensures that your crimping process meets the necessary industry standards, and provides a reference for future repairs or replacements. Proper documentation also helps maintain the ISO certified crimping process and ensures that all hydraulic hose manufacturing procedures are followed to the letter.
9. Common Mistakes to Avoid When Crimping Hydraulic Hoses
Even experienced technicians can make mistakes when crimping hydraulic hoses. Here are some of the most common mistakes and how to avoid them to ensure your hydraulic hose assembly remains strong and reliable.
9.1 Using Incompatible Components
Using incompatible hydraulic fittings or hydraulic hose materials can result in a weak connection and poor performance. Always ensure that the hydraulic hose design matches the specifications of the hydraulic fittings to prevent issues like hydraulic fluid leakage or hose failure. Verify that all components are compatible before beginning the crimping process.
9.2 Incorrect Hose Length and Fitting Selection
Choosing the wrong hose length or fitting size is another common mistake that can compromise the crimp. Always measure and select the appropriate hydraulic hose and fittings based on the system’s requirements. Proper hose installation procedures are essential for avoiding problems like hose kinks or leaks, which can result in a loss of pressure.
9.3 Failing to Perform Proper Inspections
Skipping the inspection phase after crimping can lead to overlooked defects that may cause issues later on. Always perform a thorough hydraulic hose inspection after every crimp, checking for proper alignment, smooth compression, and secure fitting. Skipping this step can result in premature hydraulic hose failure and unnecessary downtime.
10. Best Practices for Maintaining Crimped Hydraulic Hoses
Regular maintenance is essential for ensuring the longevity and performance of your hydraulic hose assembly. By following these best practices, you can prevent costly repairs and keep your hydraulic systems running smoothly.
10.1 Regular Inspection Schedules: What to Look For
Implement a regular inspection schedule to check for signs of wear, such as cracks, abrasions, or leaks. Early detection of potential issues can help extend the lifespan of your hydraulic hoses and prevent catastrophic failures. Look for visible damage on both the hydraulic fittings and hose to ensure a secure connection.
10.2 Storing Hydraulic Hoses Properly to Avoid Damage
Proper storage is essential for maintaining the integrity of hydraulic hoses. Store hoses in a cool, dry area, away from UV rays and extreme temperatures. Avoid bending the hoses too much, as this can weaken them and affect the hose pressure resistance. Keeping your hydraulic hoses in top condition will help ensure they remain reliable and effective.
10.3 Cleaning and Maintaining Crimping Tools
Keeping your crimping tools in good working order is essential for performing quality hydraulic crimping. Regularly clean your tools, check for wear and tear, and ensure that crimping dies are properly maintained. This will help prevent issues during the crimping process and ensure that each crimp is uniform and secure.
11. The Role of Certifications in Crimping Hydraulic Hoses
When it comes to hydraulic hose crimping, certifications are crucial for ensuring that your hoses meet industry standards. In this section, we’ll explore the importance of certifications and how they impact the quality and safety of your hydraulic hose assembly.
11.1 Understanding SAE Standards Hydraulic Hoses
The SAE standards for hydraulic hoses outline the specific requirements for hose construction, pressure ratings, and performance. Familiarizing yourself with these standards will help you ensure that your hydraulic hose crimping process adheres to industry best practices, ensuring the durability and safety of your hoses.
11.2 The Importance of Certified Crimping Processes for Safety
Certified crimping processes are essential to ensuring that each hose assembly meets safety and quality standards. A certified crimp ensures that the hydraulic hose fitting and hose crimping collars are securely fastened, preventing hydraulic hose failure under pressure. Certification also ensures that the crimping machine and processes are aligned with international standards, such as ISO certified crimping processes.
11.3 How to Verify If Your Crimping Process Meets Industry Standards
To ensure your crimping process meets industry standards, verify that your crimping tools and techniques are certified by relevant organizations. Keeping up to date with hydraulic crimping certification and adhering to SAE and ISO standards will guarantee that your hydraulic hose assembly is safe, reliable, and durable.
12. How to Choose the Right Hydraulic Hose Crimping Service
For businesses that prefer outsourcing, selecting the right hydraulic hose crimping service is crucial to ensuring the quality and reliability of the crimped hoses. Here’s what to consider when choosing a service provider.
12.1 Factors to Consider When Outsourcing Crimping Services
When selecting a hose crimping service, consider factors such as experience, reputation, and the provider’s knowledge of hydraulic hose design and materials. Look for a service that understands the crimping process and can handle different types of hydraulic hose assemblies.
12.2 Cost vs. Quality: What Matters Most?
While cost is always a factor, quality should be your top priority when outsourcing crimping services. A poorly executed crimp can lead to hydraulic hose failure and costly repairs. Choose a service provider that offers both competitive pricing and high-quality results.
12.3 Finding a Reliable Crimping Service Provider
Look for a crimping service provider that offers certifications, maintains top-notch equipment, and has a solid track record in hydraulic hose repair and custom hydraulic hoses. A reliable provider will help ensure the success of your hydraulic hose crimping and minimize the risk of failure.
13. Conclusion
13.1 Recap of Key Takeaways
Mastering hydraulic hose crimping is essential to ensuring the longevity and safety of your hydraulic systems. From proper crimping tool selection to regular hydraulic hose inspection, every step plays a crucial role in creating secure, high-pressure connections.
13.2 Final Tips for Perfecting Your Hydraulic Hose Crimping Skills
By following the crimping process with precision and consistency, you’ll ensure that your hydraulic hose assemblies operate smoothly and efficiently. Remember to use the right materials, perform regular inspections, and follow industry standards to achieve the best results.
13.3 How Crimping Can Improve the Longevity and Performance of Hydraulic Systems
By mastering the art of crimping hydraulic hoses, you’ll improve the hose durability, prevent failures, and enhance the overall performance of your hydraulic systems. A well-executed crimping process ensures that your equipment stays in top condition for years to come.