Introduction: What Is a Hose Crimping Machine and Why You Need One
A hose crimping machine is an essential piece of hydraulic hose crimping equipment used to create a secure, leak-proof connection between hoses and fittings. The hose crimping process is vital to ensure the integrity of your hydraulic system, preventing leaks and system failures. Whether you’re working with industrial crimping machines, manual crimping machines, or an electric crimping machine, the key to achieving a flawless crimp lies in the crimping tool, proper crimping die selection, and the correct crimping pressure. The hose fitting and its compatibility with your hose material are equally important in creating a reliable hose assembly. In this article, we’ll guide you through everything you need to know about hose crimping, from setting up your crimping machine to achieving durable crimps that meet hose crimping standards.
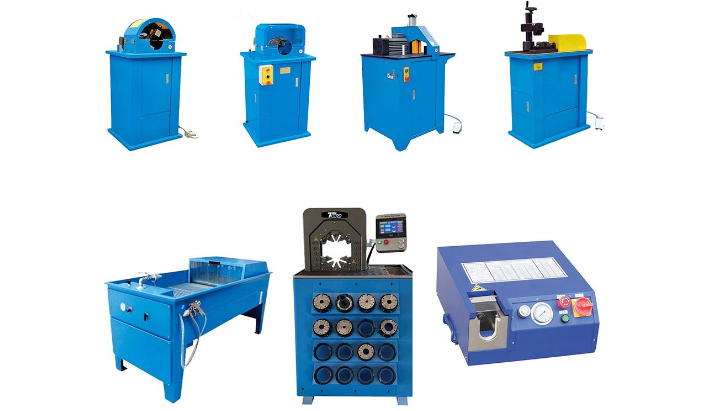
1.1 Understanding the Basics of Hose Crimping
At its core, hydraulic hose crimping involves using a crimping machine to attach a hose fitting to the end of a hose, creating a secure bond. This crimping action is done by the crimping dies inside the machine, which apply the right amount of crimping force to ensure a strong connection. Whether you are working with high-pressure hoses or low-pressure assemblies, understanding the hose material compatibility is key. Hydraulic hose maintenance involves ensuring the crimping machine is calibrated correctly for each job to guarantee quality and consistency.
1.2 The Importance of Proper Hose Crimping in Hydraulic Systems
Crimped hoses are the backbone of many hydraulic systems, and improper crimping can lead to catastrophic failures. Proper hose and fitting assembly prevents hose fitting sealing issues and ensures that your hoses maintain the required pressure, preventing dangerous leaks. The precision involved in precision crimping ensures your system operates without unnecessary downtime, which is why hose crimping machine operation must be performed correctly every time. Additionally, proper crimped hose inspection can help identify any weaknesses in the connection before they lead to system failure.
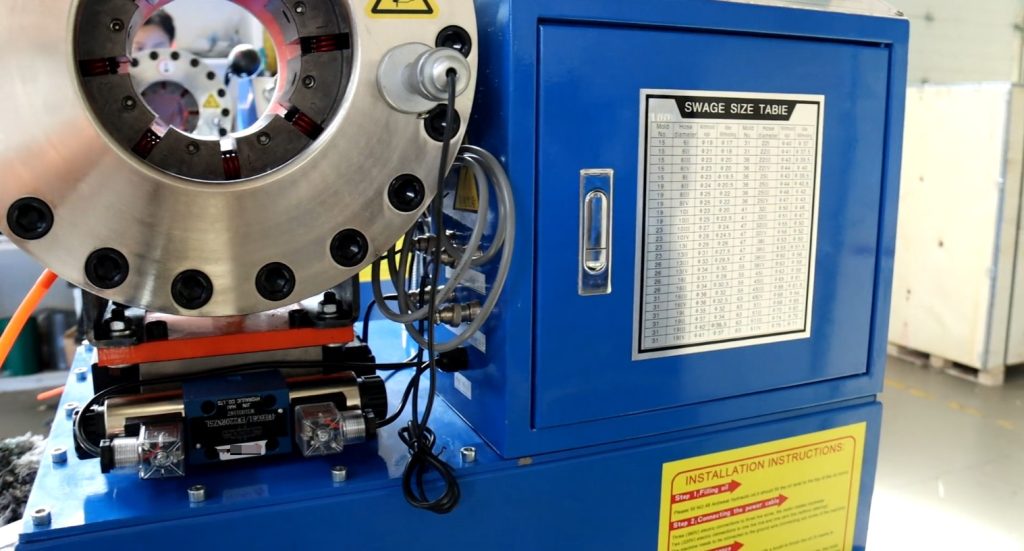
1.3 Types of Hose Crimping Machines
There are various hose crimping machine types, including manual crimping machines, electric crimping machines, and automated crimping machines. Each has its advantages depending on the scope of the job. For example, industrial hose crimping often requires the precision and power of a hydraulic crimper or industrial crimping machine, which can handle larger diameters and higher pressures. Crimping machine troubleshooting may be necessary if your crimping isn’t consistent, requiring a quick review of your crimping machine tools and crimping machine maintenance.
2. Hose Crimping Machine Components

2.1 Key Parts of a Hose Crimping Machine
The key components of any hydraulic hose crimping machine are the crimping dies, the hydraulic system (in a hydraulic crimper), and the control panel for adjusting pressure. Understanding the crimping die selection process is essential to ensure the correct size and type of die is used for each specific hose fitting. Proper maintenance of these tools helps maintain the performance of your hose crimping machine.
2.2 The Role of Dies and Tooling in Crimping
The crimping dies are one of the most critical components in the hose crimping process, as they determine the shape and size of the crimp. When selecting crimping dies, consider the hose material, size, and required pressure. Inconsistent crimped hose durability often results from incorrect die maintenance or using the wrong dies for a particular hose type. Each machine has specific die maintenance procedures to follow in order to keep the equipment working at optimal performance.
2.3 Understanding Crimping Pressure and Force
The crimping pressure is the force that the machine applies to compress the hose fitting onto the hose. This pressure needs to be calibrated properly for each application. Pressure crimping is especially crucial in high-pressure applications like high-pressure hose crimping to prevent the hose from bursting or failing under pressure. Crimping machine setup involves ensuring that the crimping machine is capable of applying the necessary force without damaging the hose.
3. Setting Up Your Hose Crimping Machine
3.1 Preparing Your Work Area for Safety and Efficiency
Before starting any hose crimping operation, ensure that your work area is set up efficiently and safely. Clear any debris, check that your crimping machine tools are in good condition, and ensure that you have the correct hose preparation materials nearby. Safety is critical—make sure that the crimping machine safety features are in place, including emergency shutdown functions.
3.2 Choosing the Right Crimping Machine for Your Needs
Choosing the correct hose crimping machine is crucial. A manual crimping machine is often used for smaller, low-volume jobs, while electric crimping machines or hydraulic crimpers are better for high-volume, industrial applications. The right machine will ensure that you get consistent and reliable crimps every time. The decision will depend on the size of the hose, the fitting material, and the volume of crimping required.
3.3 How to Install and Calibrate Crimping Dies
Installing and calibrating your crimping dies properly ensures accurate crimps. Always ensure that the die maintenance schedule is followed, and check the dies before use. Calibration is key to maintaining the right crimping cycle and crimping pressure, which can prevent inconsistent crimps and save time on repairs.
3.4 Setting the Correct Pressure and Speed for Different Hoses
To ensure the hose fitting crimping is secure, adjust the crimping pressure according to the material and diameter of the hose. The crimping cycle may need to be adjusted depending on the hose type and pressure ratings. By ensuring the correct calibration, you can prevent damage to both the hose and the fitting, especially with high-pressure hose crimping applications.
4. Selecting the Right Hose and Fittings
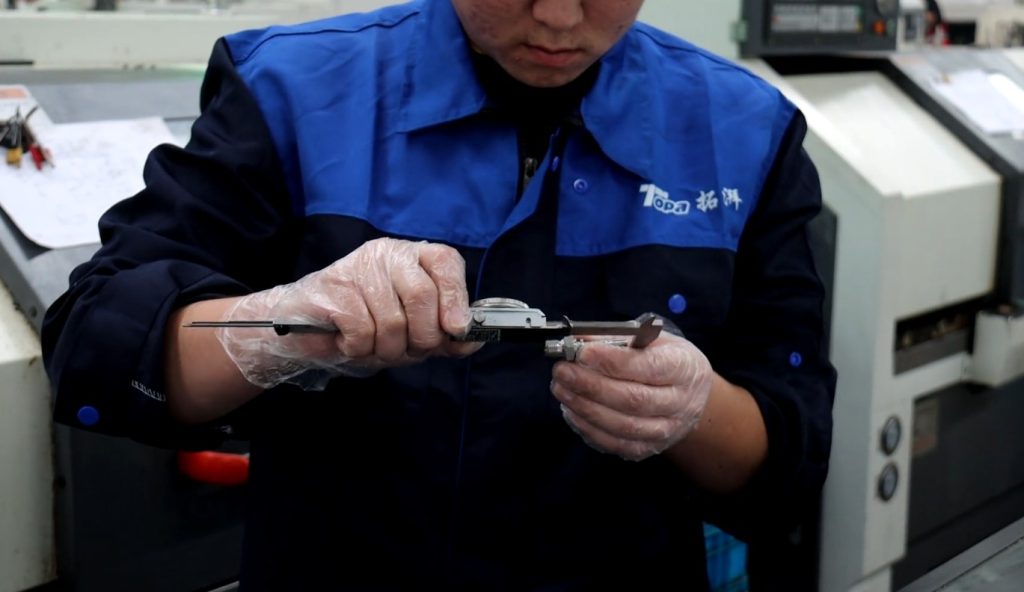
4.1 Types of Hoses Compatible with Crimping Machines
Choosing the right hose for your crimping needs involves understanding hose material compatibility. Rubber hoses, thermoplastic hoses, and steel-braided hoses each require different crimping techniques. Using the correct hydraulic hose fitting is essential for ensuring a proper seal, preventing leaks and failures.
4.2 How to Choose the Correct Fittings for Your Hose
Selecting the appropriate hose fitting is critical to achieving a durable and secure connection. Ensure that the hose fitting sealing matches the hose size and material. Consider hydraulic hose fitting installation standards to prevent leaks or failures under pressure.
4.3 Understanding Hose Compatibility and Sizing Standards
Every hose has specific size and pressure requirements. Following the proper hose crimping standards is essential to avoid misfits that could compromise the hydraulic hose quality and connection reliability. Always refer to standard sizing and fitting guidelines before beginning the crimping process.
4.4 The Role of Hose Materials in Crimping Performance
The material of the hose impacts the crimped hose durability and performance. Materials like rubber, thermoplastics, and stainless steel each have different crimping characteristics. Proper hose preparation ensures the crimp is secure and meets the required hose crimping standards.
5. Preparing the Hose for Crimping
5.1 Cutting the Hose to the Right Length
Before crimping, ensure the hose is cut to the correct length using a clean, sharp tool. Proper hose preparation prevents jagged edges, which could interfere with a smooth crimp. This is especially critical when working with high-pressure hose crimping, where precision is paramount.
5.2 Inspecting the Hose and Fittings for Defects
Check the hose and fitting assembly for any defects before crimping. Any imperfections could lead to crimping failure. Regular crimped hose inspection ensures that fittings are securely attached and that no internal or external damage is present.
5.3 Cleaning and Preparing the Hose Ends for Crimping
Clean both the inside and outside of the hose before crimping. Any contaminants, such as oil or dirt, can prevent the fitting from properly attaching to the hose, compromising the hose fitting crimping process.
6. Loading the Hose and Fitting into the Machine
6.1 Step-by-Step Guide to Properly Load the Hose
Insert the hose into the machine, ensuring it is aligned with the crimping dies. A misaligned hose can cause uneven crimping, leading to leaks or system failure. Check the alignment to ensure hose fitting sealing is correctly applied.
6.2 Ensuring Correct Alignment for a Secure Crimp
Always double-check the alignment before starting the crimp. Hose fitting crimping is most effective when both the hose and the fitting are aligned correctly. Misalignment can lead to poor hose crimping and cause leaks or fitting failure, making your connection unreliable. Ensure that the hose fitting crimping process is performed with precision to avoid costly repairs later.
6.3 Tips for Avoiding Common Loading Errors
Common mistakes when loading hoses and fittings include improper alignment or insufficient insertion depth. Always make sure that the hose fitting is fully seated in the crimping machine, and double-check the hose preparation for debris or defects. Taking a moment to verify the crimping machine setup can save time and reduce rework.
7. The Crimping Process: How to Crimp the Hose
7.1 Understanding the Crimping Cycle and Timing
The crimping cycle is the period during which the crimping machine applies pressure to the hose and fitting. Timing is essential for the quality of the crimp, as too short or too long a cycle can lead to improper crimps. By adjusting the cycle to match the hose material, you’ll ensure that the crimp is both secure and durable.
7.2 Step-by-Step Guide to Crimping a Hose Properly
Once everything is loaded correctly, initiate the crimping process by pressing the crimping button. The hydraulic hose crimping machine will apply the necessary crimping pressure to secure the fitting. As the crimping die selection plays a critical role in this, ensure the correct dies are in place to match the hose and fitting specifications. After completing the crimp, remove the crimped hose for inspection.
7.3 Adjusting Crimping Settings for Different Hose Types
Different hose types require specific settings. For example, a high-pressure hose crimping application will require a different crimping force than a regular industrial hose. Adjust the pressure and speed settings of your crimping machine according to the hose’s material and intended use. Fine-tuning these settings ensures the best results for each job.
7.4 Visual Indicators of a Successful Crimp
After completing the crimp, conduct a crimped hose inspection to ensure the crimp is secure and uniform. A well-done crimp should have no gaps or uneven pressure marks. The fitting should be firmly attached to the hose, ensuring that the hose fitting sealing is tight and leak-proof. If you notice any issues, consider adjusting your crimping pressure or die maintenance.
8. Troubleshooting Common Crimping Issues
8.1 Identifying and Fixing Incorrect Crimps
If your crimps are not holding or appear damaged, it’s important to diagnose the issue quickly. Crimping machine troubleshooting may reveal common issues such as insufficient crimping pressure or incorrect die selection. Check the machine settings and inspect the fittings and hoses to ensure they meet the required standards for hose crimping quality.
8.2 Dealing with Misalignment or Pressure Issues
Misalignment is a common issue that leads to poor crimps. Ensure that the hose and fitting assembly is properly aligned before beginning the crimping process. If you suspect pressure problems, verify the hydraulic crimping pressure and adjust the machine accordingly. Proper calibration of the crimping machine setup is crucial to avoid these issues.
8.3 How to Fix Fitting Slippage and Hose Damage
If your hose fitting is slipping or the hose shows signs of damage after crimping, this could be due to incorrect crimping pressure or poor alignment during loading. Recheck the hose fitting sealing process, ensuring the fitting is firmly pressed onto the hose without excessive force. In cases of damage, re-examine the crimping machine tools and consider performing a crimping machine maintenance check.
9. Post-Crimping Inspection: Ensuring Quality and Durability
9.1 How to Inspect Crimped Hoses for Quality
Once you’ve completed the crimp, perform a thorough inspection to ensure the connection is secure. A proper inspection should focus on the uniformity of the crimp, ensuring there are no gaps or uneven crimps. Checking for crimped hose durability is essential to confirm that the connection can withstand the pressures and demands of the system.
9.2 Visual and Mechanical Checks for a Perfect Crimp
Visually inspect the crimp for any defects, but also perform mechanical checks. Using a pull test or pressure test will ensure the hose and fitting are securely crimped. This can be especially useful when performing pressure crimping for high-demand systems where hose and fitting failure can be catastrophic.
9.3 Ensuring Compliance with Industry Standards
Ensure that your crimps meet hose crimping standards for the specific application. Compliance with industry regulations like SAE or DIN ensures that your crimped hose connections meet safety and performance requirements. Always verify the crimp meets the necessary standards to ensure the hydraulic hose fitting installation is done correctly.
10. Maintenance Tips for a Long-Lasting Crimping Machine
10.1 Routine Cleaning and Care for the Crimping Machine
Regular maintenance of your crimping machine tools is essential for long-term performance. Ensure that the crimping machine is cleaned thoroughly after each use to remove dirt, oil, or debris that can affect crimp quality. Keeping the machine in optimal condition helps prevent breakdowns and extends the lifespan of the equipment.
10.2 How to Maintain Dies and Tools for Optimal Performance
The crimping dies and tools play a vital role in the crimping process. Over time, these tools may experience wear, affecting the quality of the crimps. Regularly check the die maintenance and replace any worn-out parts to ensure your crimps are consistent and high-quality. Keeping your hydraulic hose crimping machine in good condition is essential for smooth operation.
10.3 Preventing Wear and Tear: Best Practices for Machine Longevity
Properly maintaining your crimping machine can prevent unnecessary wear and extend its lifespan. Follow the manufacturer’s maintenance guidelines, including checking for loose components and ensuring that all parts are properly lubricated. Regular inspections will also help catch any issues before they cause major downtime.
11. Safety Precautions When Using a Hose Crimping Machine
11.1 Essential Safety Gear and Protective Equipment
Always wear the appropriate safety gear when operating a hydraulic hose crimping machine. This includes gloves, safety glasses, and steel-toed boots. These precautions will protect you from flying debris or unexpected machine malfunctions.
11.2 Best Practices to Avoid Injury During Operation
Safety during hose crimping involves following machine operation protocols. Avoid placing hands near the crimping dies while the machine is in operation. Always engage the safety mechanisms in the machine and be aware of your surroundings to prevent accidents.
11.3 Emergency Shutdown Procedures and Safety Protocols
Be familiar with the crimping machine operation and emergency shutdown procedures in case something goes wrong. Keep emergency buttons accessible and make sure the work area is clear of obstructions to ensure a quick response in case of emergency.
12. The Benefits of Automated Hose Crimping Machines
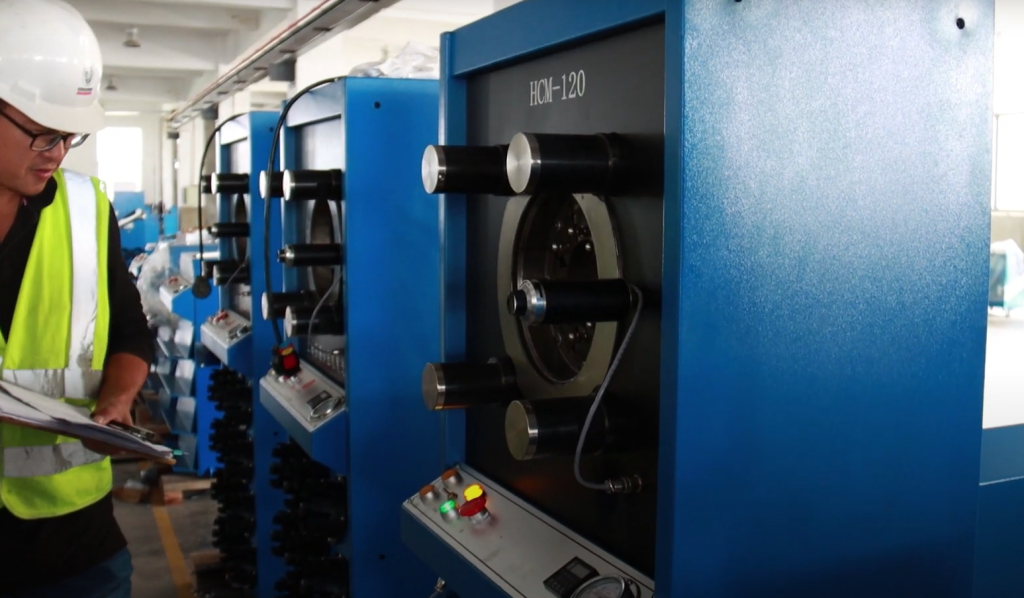
12.1 How Automation Improves Efficiency and Precision
Automated hose crimping machines significantly improve efficiency, speed, and precision. By eliminating manual adjustments, automated systems provide consistent, high-quality crimps every time. This is especially useful in high-volume environments where fast, precise industrial hose crimping is essential.
12.2 Reducing Human Error in Hose Crimping
Automated crimping machines reduce the likelihood of human error, ensuring that each crimp is uniform and meets quality standards. Automation allows for consistent crimping pressure and correct crimping die selection, eliminating variability that can occur with manual processes.
12.3 Saving Time and Increasing Output with Automated Machines
Using automated crimping machines leads to faster production cycles and a higher output of finished hoses. This increase in productivity is particularly valuable for operations that require hose crimping for machinery or need to fulfill high-demand orders.
13. Advanced Tips for Professional Hose Crimping
13.1 Using Advanced Features on High-End Crimping Machines
High-end crimping machines come with advanced features like automatic calibration, multi-die systems, and data logging, which enhance the precision of crimps. These features make the crimping process more efficient and accurate, particularly when working with a variety of hose sizes and materials.
13.2 How to Handle Special Materials and High-Pressure Hoses
When working with high-pressure hose crimping, adjust your settings to accommodate the specific requirements of the material. For instance, you may need to use more crimping pressure and slower crimping cycles to ensure that the crimp is tight and secure without damaging the hose.
14. Troubleshooting and Repairing Your Crimping Machine
14.1 How to Identify When Your Crimping Machine Needs Repair
If your crimping machine starts showing signs of inconsistent crimps or operational issues, it may be time to perform a repair. Check for problems with the hydraulic crimping pressure, die maintenance, or any mechanical failures within the machine.
14.2 Common Issues and How to Fix Them
Common problems include inaccurate crimps, machine malfunction, or misalignment. If these occur, check the crimping machine tools, the crimping dies, and ensure the machine is properly calibrated for the job at hand.
14.3 When to Call in a Professional Technician
If your crimping machine is still malfunctioning after troubleshooting, it may be time to call in a professional. A technician can provide expert advice and perform any necessary repairs to ensure your hose crimping machine operates at peak efficiency.
15. Conclusion: Mastering Hose Crimping for Efficiency and Quality
15.1 Recap of Key Hose Crimping Tips
Mastering the art of hose crimping requires practice, precision, and the right tools. By following the correct crimping machine setup, ensuring proper die maintenance, and using the correct crimping pressure, you can achieve consistent, high-quality crimps.
15.2 Final Thoughts on Perfecting Your Crimping Skills
Perfecting your crimping skills enhances your ability to work efficiently and safely. Whether you’re crimping hoses for industrial machinery or high-pressure systems, proper training and machine setup are crucial.
15.3 How to Maximize the Performance of Your Hose Crimping Machine
By investing time in machine maintenance, crimping machine troubleshooting, and continuous improvement of your crimping technique, you can maximize the lifespan and performance of your hose crimping machine, ensuring reliable hose connections for years to come.