1. Introduction to Hydraulic Hose Crimping
Hydraulic systems power some of the most demanding industries, from construction and agriculture to manufacturing and transportation. These systems rely on strong, high-pressure connections to perform efficiently. But what happens when a connection fails? A tiny leak can bring a massive machine to a grinding halt, resulting in costly downtime, safety risks, and expensive repairs. That’s where a hydraulic hose crimping tool comes in—a crucial piece of hydraulic equipment that ensures your hydraulic hose fittings are secured with precision, providing a leak-proof connection that withstands extreme pressures.
In this guide, we’ll walk you through everything you need to know about using a crimping machine, step by step. Whether you’re an experienced technician or a beginner, mastering this crimping process will make your hose assembly more reliable, safer, and longer-lasting.

2. Understanding the Components of a Hydraulic Hose Crimping Tool
Before you start industrial hose crimping, it’s important to understand the essential parts of the hydraulic hose crimper and how they work together. Each component plays a critical role in creating a secure high-pressure hose connection.
2.1 Crimping Machine Types: Manual, Electric, and Portable
There are three main types of professional crimping tools—manual crimping tools, electric crimping tools, and portable crimping tools.
- Manual crimping tools are lightweight and ideal for smaller jobs, including field repairs.
- Electric crimping machines are perfect for high-volume jobs that require consistent pressure for large hose assemblies.
- Portable crimping tools are excellent for on-site hydraulic hose repair, offering convenience and flexibility for field technicians.
2.2 Key Parts of a Crimping Tool: Dies, Press, and Calibration System
A crimping tool consists of several key components:
- Crimping dies: These interchangeable pieces determine the size of the crimp.
- Hydraulic press: The press applies the necessary force to reshape the hydraulic fittings.
- Crimping tool calibration: Ensures that the hose crimper dies apply the correct amount of pressure for a secure crimp.
2.3 Safety Features and Precautions Built into Crimping Tools
Modern industrial crimping machines come with safety features like crimping tool safety tips, automatic shut-offs, and overload protection to prevent damage to the hydraulic hose equipment and ensure the safety of users.
3. Preparing for the Crimping Process
Preparation is key to achieving a perfect crimp. Taking the time to measure, cut, and clean your hose ensures a secure and durable hydraulic hose assembly.
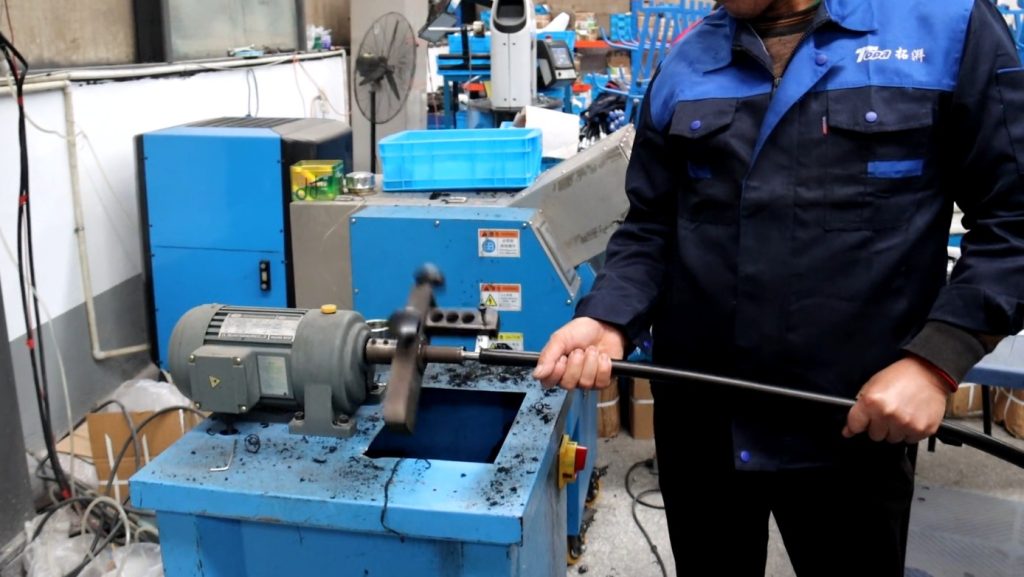
3.1 Selecting the Right Hydraulic Hose and Fittings
Choosing the correct hydraulic hose sizes and hydraulic fitting types for your hydraulic hose installation is essential to ensure compatibility and avoid hydraulic hose leaks.
3.2 Measuring and Cutting the Hose to the Correct Length
Using a hose cutting tool to make a clean, precise cut is crucial for ensuring that the hydraulic hose sealing solutions work effectively.
3.3 Cleaning and Inspecting the Hose and Fittings
Always inspect the hydraulic hose durability to ensure there are no signs of damage. Proper cleaning is essential to maintain hydraulic system efficiency.
4. Choosing the Right Crimping Dies
Selecting the correct crimping dies is essential for achieving a uniform, secure crimp.

4.1 What Are Dies and How Do They Work?
Crimping dies reshape the fitting during the hose assembly process, ensuring a tight seal that withstands pressure.
4.2 How to Match Dies to Hose Sizes and Materials
Matching hose crimper dies to the right hydraulic hose compatibility is key to preventing hose crimping mistakes and ensuring hydraulic hose safety.
4.3 Tips for Proper Die Storage and Maintenance
To keep your crimping machine in top condition, follow regular crimping tool maintenance practices, including storing dies properly to prevent damage.

5. Step-by-Step Guide to Using a Hydraulic Crimping Tool
Let’s dive into the crimping tool setup with a detailed guide.
5.1 Setting Up the Crimping Machine
Ensure your field crimping tool is properly calibrated, and select the correct crimping dies for your hydraulic hose standards.
5.2 Inserting the Hose and Fitting into the Die
Carefully insert the hydraulic fitting types and high-pressure hose into the hose crimper dies.
5.3 Performing the Crimping Operation
Activate the hydraulic press to perform the crimp. Follow proper crimping techniques to avoid errors.
5.4 Inspecting the Crimp for Quality Control
Inspect your hydraulic hose sealing to ensure the crimp is even and secure, reducing the risk of hydraulic hose leaks.
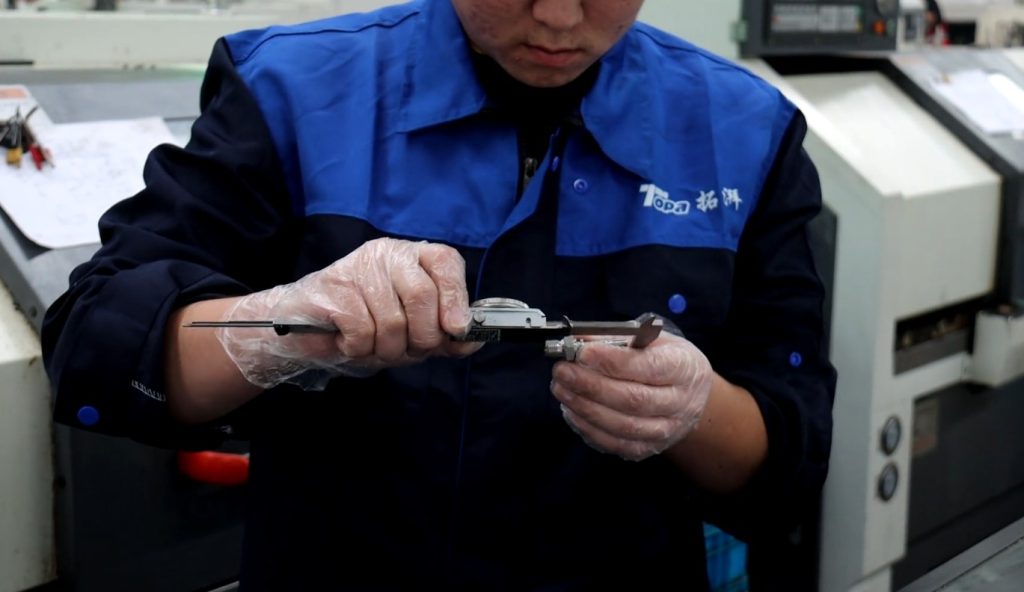
6. Common Crimping Mistakes and How to Avoid Them
Even experienced technicians make mistakes. Here’s how to avoid common hose crimping mistakes.
6.1 Over-Crimping and Its Consequences
Over-crimping damages the hydraulic hose fittings and reduces the hose’s lifespan.
6.2 Under-Crimping and How It Leads to Leaks
Under-crimping results in loose connections, leading to hydraulic hose leaks.
6.3 Misalignment of the Hose and Fittings
Proper crimping tool calibration prevents misalignment and ensures best practices for crimping.
7. Testing the Crimped Hose for Durability
After heavy-duty hydraulic crimping, test the hose for hydraulic hose durability.
7.1 Pressure Testing: Ensuring the Hose Can Handle High Pressure
Perform hose pressure testing using hydraulic pressure testing equipment to verify the crimp’s strength.
7.2 Visual Inspection for Cracks and Imperfections
Look for signs of wear and cracks during the hydraulic hose inspection.
7.3 Functional Testing in Real-World Scenarios
Install the hose and monitor it to ensure it performs as expected under high-pressure connections.
8. Maintaining Your Crimping Tool for Long-Term Use
Proper crimping tool maintenance ensures your tool’s longevity.
8.1 Regular Cleaning and Lubrication
Regularly clean and lubricate your crimping machine to maintain performance.
8.2 Checking for Wear and Tear on Dies and Components
Inspect the crimping tool accessories for wear to ensure consistent results.
8.3 Recalibrating the Machine for Precision
Regular crimping tool troubleshooting and calibration are essential for achieving hydraulic coupling types that last.
9. Troubleshooting Common Hydraulic Hose Crimping Issues
Even the most experienced professionals encounter issues during hydraulic hose assembly. Here’s how to troubleshoot common problems and get back to work quickly.
9.1 The Hose Slips During Crimping
If the hose slips during crimping, it’s often a sign that the hydraulic fitting types and the hose crimper dies aren’t correctly aligned. Ensure the hose is securely placed in the crimping machine before applying pressure.
9.2 Uneven Crimps and How to Fix Them
Uneven crimps can lead to leaks and unreliable connections. This could be due to worn-out crimping dies or improper crimping tool setup. Regularly inspect and replace crimping tool accessories when necessary.
9.3 Machine Malfunctions: When to Call a Technician
If your electric crimping tool or manual crimping tool isn’t working properly, check for any obvious signs of wear or mechanical failure. When in doubt, consult the crimping tool instructions and call a professional technician for hydraulic system troubleshooting.
10. Safety Tips for Using a Crimping Tool
Safety should always be a priority when using hydraulic tools. Here are some essential crimping tool safety tips to prevent accidents.
10.1 Personal Protective Equipment (PPE) to Wear
Wear PPE such as gloves, goggles, and steel-toed boots to protect yourself from flying debris and accidental hydraulic leaks during the hydraulic hose installation process.
10.2 Safe Handling of Hydraulic Hoses and Tools
Properly handle all hydraulic hose equipment to avoid damage to both the hoses and the crimping tool. Ensure that all hydraulic hose fittings are securely installed before starting any crimping.
10.3 Emergency Procedures in Case of Malfunctions
If your crimping machine fails mid-operation, turn off the power immediately. Hydraulic hose repair should only be done once the system is depressurized to prevent accidents and ensure crimping tool calibration is accurate.
11. Benefits of Proper Crimping in Hydraulic Systems
Hydraulic system maintenance requires attention to detail, and proper crimping techniques provide long-lasting benefits for your machinery.
11.1 Increased Hose Longevity and Reliability
Well-crimped hoses will perform better and last longer, reducing the frequency of hydraulic hose replacement and improving overall hydraulic system efficiency.
11.2 Reduced Risk of Hydraulic Failures
By ensuring all connections are securely crimped, you’ll minimize the risk of leaks and failures in the system, thus avoiding costly repairs and downtime.
11.3 Cost Savings from Fewer Replacements
Investing in high-quality crimping tools and proper hydraulic hose sealing techniques can save money in the long run by preventing hydraulic hose leaks and the need for frequent replacements.
12. How to Choose the Best Hydraulic Crimping Tool for Your Needs
Selecting the right crimping tool can be the difference between a secure, leak-free connection and a failed one. Here are some tips on how to choose the best crimping machine for your needs.
12.1 Factors to Consider: Size, Power, and Portability
When selecting a portable crimping tool, consider the hydraulic hose sizes you typically work with, the hydraulic press’s maximum crimping capacity, and whether you need a battery-powered crimper for portability.
12.2 Recommended Brands and Models
Some of the best crimping machine brands include Parker crimper, Gates hydraulic crimper, Finn-Power crimper, and Eaton Weatherhead crimper. These brands are known for their reliability and precision in heavy-duty hydraulic crimping.
12.3 Comparing Costs and Features
When comparing hydraulic crimping tools, be sure to look at factors like ease of use, accuracy, and warranty. Professional crimping tools often come with added features, such as crimping tool accessories, that can improve your efficiency.
13. Crimping Different Types of Hydraulic Hoses
Each type of hose requires a different approach. Here’s how to tackle crimping for various hydraulic hose applications.
13.1 Crimping Steel Braided Hoses
Steel braided hoses require careful hose cutting and selection of the right crimping dies to prevent damaging the braiding during the crimping process. Use the appropriate crimping tool guide for steel hoses.
13.2 Crimping Textile-Reinforced Hoses
Textile-reinforced hoses are more flexible but still require precision. Ensure your hydraulic hose crimping tool can handle the soft inner lining without causing leaks.
13.3 Crimping Thermoplastic Hoses
Thermoplastic hoses are used in specific applications requiring hydraulic fluid compatibility. Choose high-pressure fittings that match the material type to prevent failure in demanding environments.
14. Industry Standards and Certifications for Crimped Hoses
To ensure your hose connections meet industry standards, it’s important to be familiar with crimping certification and regulatory requirements.
14.1 ISO and SAE Standards for Hydraulic Hoses
The hydraulic hose standards set by organizations like ISO and SAE ensure that crimped hoses meet safety and performance requirements for a wide range of industries.
14.2 How to Ensure Your Crimps Meet Industry Requirements
Make sure your crimping machine is calibrated according to the latest hose fitting standards and crimping tool calibration methods. This will ensure your hoses are compliant with safety regulations.
14.3 The Importance of Certified Crimping Machines
Using a certified industrial crimping machine ensures the integrity of your hydraulic system, providing peace of mind that the hose assembly can handle high pressures and extreme conditions without failing.
15. FAQs About Hydraulic Hose Crimping
15.1 How Long Does a Crimped Hose Last?
With proper hydraulic hose maintenance tips, crimped hoses can last for years. Regular hydraulic hose inspection and maintenance help extend their service life.
15.2 Can You Reuse Crimped Fittings?
No, crimped fittings are generally not reusable. Reusing hydraulic hose fittings can lead to leaks and system failures, so always replace fittings when performing hydraulic hose repair.
15.3 What to Do If a Crimped Hose Leaks?
If a crimped hose leaks, first inspect the hose crimping process to ensure the crimp was performed correctly. If the crimping was done properly but the hose still leaks, check for other issues like hydraulic hose compatibility or wear and tear.
16. Final Thoughts and Best Practices for Successful Crimping
Mastering the hydraulic hose crimping tool is essential for anyone working with hydraulic systems. By following the tips and guidelines provided here, you’ll be able to create secure, high-pressure connections that are safe, reliable, and durable. Proper crimping tool maintenance, attention to detail during the hose assembly process, and choosing the best crimping machine will go a long way toward improving hydraulic system efficiency and avoiding costly mistakes.