1. Introduction to Hydraulic Hose Crimpers
Hydraulic systems are everywhere—from heavy-duty construction equipment to the intricate machinery that powers automotive industries. And yet, behind these complex systems lies a simple but critical component: the hydraulic crimping tool. At first glance, this might seem like just another industrial tool, but in reality, it plays a vital role in ensuring that hydraulic hose fittings are properly attached, sealed, and able to withstand intense pressure. Without the proper hose crimping machine, the entire hydraulic system would be at risk of failure, causing downtime and expensive repairs. In this article, we’ll break down the purpose of hydraulic hose crippers, explore the different types available, and explain why they’re absolutely essential for industries that rely on hydraulic systems. Ready to uncover the power behind this crucial tool? Let’s dive in!
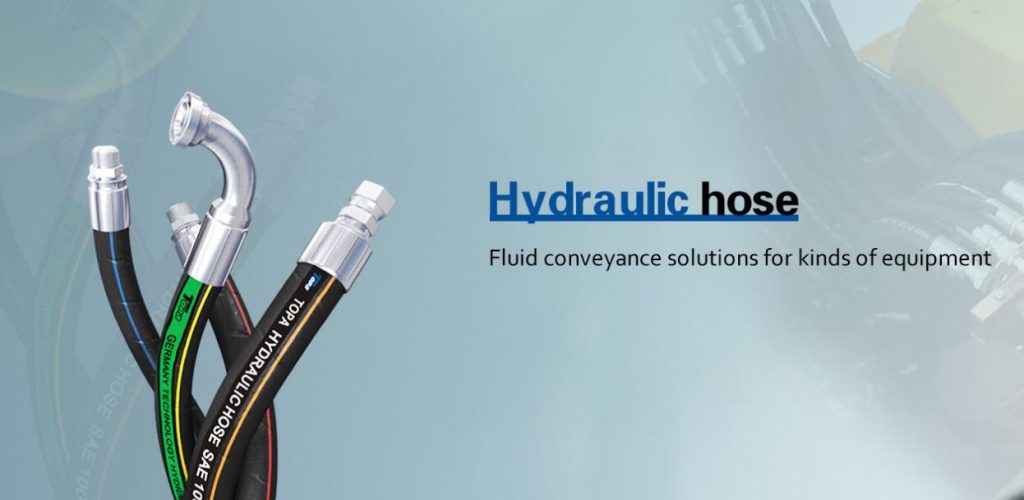
1.1 What is a Hydraulic Hose Crimper?
A hydraulic hose crimper is a machine used to attach hydraulic hose assemblies by compressing the hose around a hydraulic fitting to create a secure, leak-proof connection. The crimping process involves using mechanical force, often with a hose crimping die, to secure the fitting firmly to the hose. This is a crucial step in ensuring that hydraulic hose pressure is properly managed within the system. The tool uses precision and high force to guarantee that the hydraulic hose connection is durable, ensuring the system operates under high pressure without failure. Whether in construction or automotive industries, hose crimping accuracy ensures systems function flawlessly under intense stress.
1.2 Why Hydraulic Hose Crimpers are Essential in the Industry
In the world of hydraulic hose manufacturing, precision and reliability are non-negotiable. A poorly crimped hose can lead to catastrophic failures, causing everything from minor leaks to major system breakdowns. This is where industrial hose crimpers come in. These machines ensure that the hose fitting connection is perfectly sealed, which is crucial for the safe and efficient operation of machinery. Without the right crimper, hydraulic hose leak prevention becomes almost impossible. Industries like construction, agriculture, and aerospace depend on crimping technology to keep systems sealed and operating efficiently. From hydraulic hose sealing to ensuring hoses can handle high-pressure hoses, these tools play a cornerstone role in the industrial world.
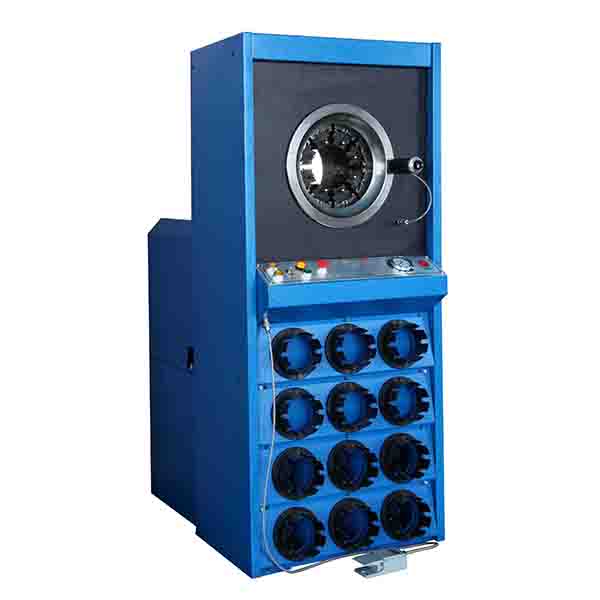
2. Understanding the Hydraulic Hose Crimping Process
The hose crimping process isn’t just about squeezing a hose and fitting together—it’s a carefully controlled procedure that requires precision, knowledge, and the right crimping tools. When crimping, it’s not only the size and pressure of the crimp that matters, but also how evenly it’s applied across the fitting. A successful crimp ensures that the hose fitting remains attached to the hose without any chance of slipping or leaking, even under high pressure. Let’s dive deeper into the science behind this process.
2.1 The Science Behind Hose Crimping
Hydraulic crimping involves using mechanical force to deform the hose and the fitting, creating a tight connection. This force is usually applied through a hose press, hose crimping equipment, or a hose crimper machine. The key to successful crimping is achieving the correct amount of compression, which requires the right balance of pressure, tool settings, and material compatibility. If the hose is crimped too tightly, it could damage the hose or fitting; too loosely, and it won’t provide a secure seal. Crimping tool performance is essential in ensuring that every connection is reliable and secure under intense hydraulic hose pressure. The right crimping dies and crimping fitting tools ensure the best outcome for every application.
2.2 Key Components of a Hydraulic Hose Crimping Machine
Crimping machines for hoses are made up of several critical components, each playing a role in ensuring a perfect crimp. The crimping die is one of the most important parts, and it comes in various sizes to accommodate different hose diameters and fittings. Other components include the hydraulic crimping machines’ pressure system, which generates the hydraulic force needed to apply the crimp, and the control panel, which allows the operator to set and monitor crimping parameters. These elements must work together seamlessly to ensure a high-quality result every time.
3. Types of Hydraulic Hose Crimpers
There’s no one-size-fits-all when it comes to hydraulic crimping machines. Depending on the application, work environment, and specific needs of a business, different types of crimpers may be used. Let’s take a look at the various types of hydraulic crimpers available on the market.
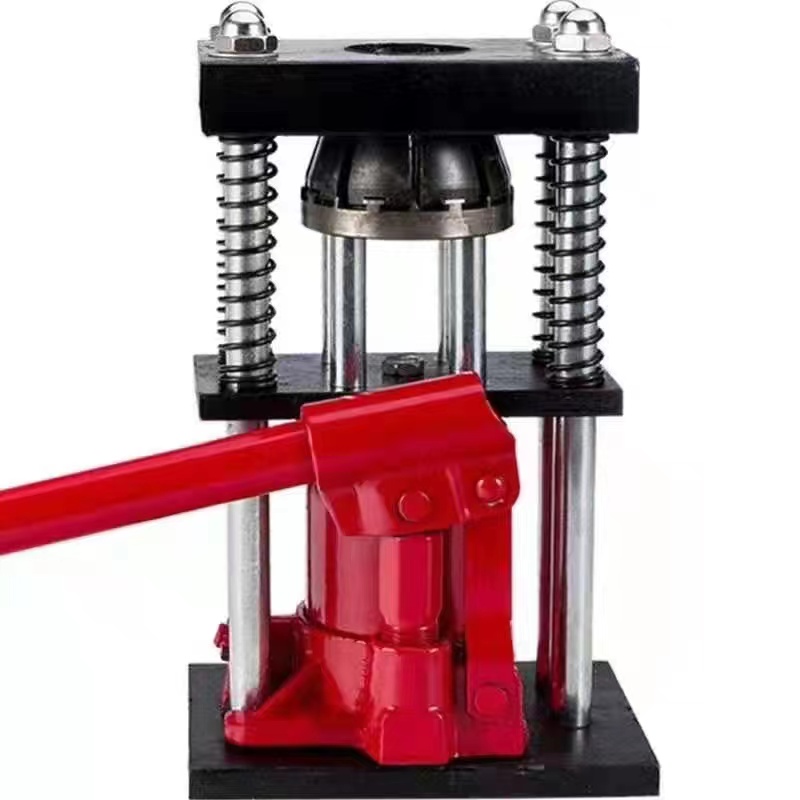
3.1 Manual Crimpers
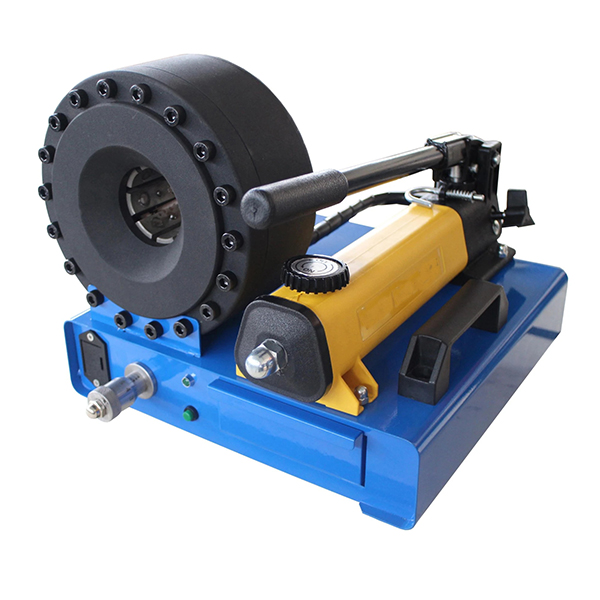
Manual crimpers are the simplest and most cost-effective type of crimper. They are operated by hand and rely on mechanical force to crimp the hose and fitting. Manual crimpers are typically used for small-scale operations or situations where portability is key. However, they require more effort and time than powered crimpers, and they may not be suitable for larger jobs or high-volume production environments.
3.1.1 How Manual Crimpers Work
Manual crimpers use a pair of handles or levers to apply force to the crimping dies. The user places the hose and fitting into the die, then squeezes the handles together, which pushes the die together and compresses the hose onto the fitting. The amount of force needed will depend on the material and size of the hose, but generally, the operator must apply enough pressure to create a secure seal.
3.1.2 Advantages and Disadvantages of Manual Crimpers
Manual crimpers are low-cost and portable, making them an attractive option for small businesses or mobile technicians. However, they can be physically demanding and may not offer the same level of precision as powered models. They also tend to be slower and less suitable for high-volume operations.
3.2 Hydraulic Crimpers
Hydraulic crimpers use hydraulic power to apply force, making them much more efficient than manual crimpers. These crimpers are capable of handling larger jobs and providing more consistent results with less physical effort from the operator. Hydraulic hose crimping tools are ideal for medium to large-scale operations, as they provide a good balance between power and precision.
3.2.1 The Role of Hydraulic Power in Crimping
The hydraulic system in these crimpers uses pressurized fluid to create force, which is applied to the crimping die. The fluid pressure allows the crimper to handle more substantial and heavier-duty hoses with greater ease. This makes hydraulic crimping tools an excellent choice for operations requiring high volume and consistent performance.
3.2.2 Pros and Cons of Hydraulic Crimpers
Hydraulic crimpers offer significant power and precision, making them ideal for larger-scale operations. However, they tend to be more expensive and bulkier compared to manual crimpers. They also require a source of hydraulic power, which may not be available in all work environments.
3.3 Electric Crimpers
Electric crimpers combine the precision of hydraulic crimping crimpers with the convenience of electric power. These crimpers are highly efficient and can be used in settings where hydraulic power is unavailable or impractical. They are commonly used in industrial hose crimpers applications like automotive and aerospace.
3.3.1 How Electric Crimpers Stand Out
Electric crimpers operate by using an electric motor to drive the crimping mechanism. This allows for quick, consistent crimps without requiring manual labor or hydraulic power. They are fast, precise, and relatively easy to operate, making them ideal for high-volume production.
3.3.2 When to Choose an Electric Crimper
Electric crimpers are perfect for businesses with high production demands where speed and precision are essential. They are also great for shops that do not have access to hydraulic power but still need a machine capable of handling a wide range of hose fitting sizes.
3.4 Pneumatic Crimpers
Pneumatic crimpers operate using compressed air instead of hydraulic fluid or electricity. These crimpers offer a high level of precision and speed, making them a popular choice in industries like automotive repair and manufacturing.
3.4.1 What Makes Pneumatic Crimpers Unique?
Pneumatic crimpers are powered by air pressure, which makes them ideal for environments where hydraulic or electric power is unavailable. They are lightweight, portable, and relatively easy to maintain, providing a great option for shops that need flexibility and efficiency.
3.4.2 Benefits of Pneumatic Crimping Machines
Pneumatic crimpers are energy-efficient, fast, and less bulky than hydraulic machines. They are perfect for smaller operations or those that require a high degree of portability and ease of use.
4. Key Features to Look for in a Hydraulic Hose Crimper
When selecting a hydraulic hose crimper, there are several factors to consider. The right crimper will help you achieve the perfect crimp every time, ensuring that your hydraulic hose installation is reliable and effective. Here are the key features to look for:
4.1 Crimp Range and Capacity
The crimp range refers to the size of the hose and fitting that the machine can handle. It’s essential to choose a crimper that can handle the range of hoses you plan to work with.
4.2 Precision and Accuracy in Crimping
Precision is crucial in ensuring that each crimp is done correctly. A crimper with adjustable pressure settings and accurate die alignment can help achieve the best results for hydraulic hose sealing and pressure resistance.
4.3 Durability and Build Quality
A well-built crimper should withstand constant use without showing signs of wear or performance decline. Look for machines with robust materials that are designed for long-lasting operation.
4.4 Ease of Use and Maintenance
Look for crimpers that are easy to operate and maintain. A user-friendly interface and simple maintenance routine will save you time and effort in the long run.
4.5 Portability and Space Efficiency
If you’re operating in a confined space or require a mobile setup, a portable and compact crimper is ideal. These machines are easy to store and transport, offering flexibility without compromising on performance.
5. The Importance of Choosing the Right Crimper
Choosing the right hydraulic crimper can significantly impact the efficiency, safety, and cost-effectiveness of your operation. The wrong crimper can lead to faulty hose connections, frequent repairs, and delays that could have been avoided with the proper tool.
5.1 Matching the Right Crimper to Your Hose and Fittings
It’s essential to select a crimping machine for hoses that fits your specific hose fitting connection needs. Not all crimpers are suited for every type of hose, so understanding the compatibility is key.
5.2 The Cost-Effectiveness of Choosing the Right Tool
While a high-quality crimper might require a higher initial investment, it can save you money in the long run by reducing the risk of hose failures, downtime, and costly repairs.
6. How to Operate a Hydraulic Hose Crimper
Operating a hydraulic hose crimper involves a series of steps that ensure a perfect, secure crimp every time. Here’s a guide to help you navigate the process efficiently and safely.
6.1 Step-by-Step Guide to Using a Crimper
- Prepare the Hose and Fitting: Ensure the hose is cut cleanly and the fitting is aligned properly.
- Set the Crimper: Adjust the crimping machine to the desired settings based on the hose and fitting size.
- Load the Hose into the Crimper: Place the hose and fitting into the crimping die.
- Apply the Crimp: Activate the machine, either manually, hydraulically, or electrically, to apply the crimping force.
- Inspect the Crimp: Check the crimp for any signs of over-crimping or under-crimping.
6.2 Safety Precautions When Operating a Crimper
Always wear appropriate protective gear, such as gloves and safety glasses, and ensure the crimper is properly calibrated before use. Follow manufacturer guidelines and avoid bypassing safety features.
6.3 Troubleshooting Common Crimping Issues
If you notice issues like leaks or loose fittings, check for problems such as incorrect settings, faulty crimping dies, or worn-out components. Regular maintenance and inspection can help prevent these issues.
7. The Role of Hydraulic Hose Crimpers in Various Industries
From construction sites to manufacturing plants, hydraulic hose crimpers are found in countless industries. They ensure that equipment runs smoothly and safely by creating secure, pressure-resistant hose connections. Let’s take a look at how these machines are used in different fields.
7.1 Hydraulic Hose Crimpers in Construction
In construction, hydraulic hoses are used to power heavy machinery, such as excavators and bulldozers. Crimping machine operation ensures that these hoses remain intact under extreme pressure, preventing costly breakdowns.
7.2 Applications in Automotive and Aerospace
The automotive and aerospace industries rely on hydraulic hose crimping techniques to ensure that fuel, brake, and other critical systems function flawlessly, even under the most demanding conditions.
7.3 Crimping in Agriculture and Manufacturing
Industrial hydraulic crimpers are essential in agricultural equipment, where they ensure smooth operation of irrigation systems, tractors, and harvesters, even in harsh environments.
7.4 The Importance of Crimpers in Oil and Gas Industry
The oil and gas industry relies on hydraulic systems to control drilling, pumping, and transport processes. Crimping ensures that these systems remain safe and leak-free, even in high-pressure situations.
8. Maintenance and Care of Hydraulic Hose Crimpers
Maintaining your hydraulic hose crimper is essential for long-term reliability and performance. Regular care ensures that the machine stays in top condition, minimizing the risk of malfunctions and downtime.
8.1 Regular Cleaning and Inspection Tips
Clean the crimper regularly to remove debris and check for signs of wear. This includes inspecting the hydraulic crimping machine parts, crimping dies, and hose crimping equipment.
8.2 Replacing Worn-out Dies and Parts
As with any piece of machinery, certain parts of the crimper will wear out over time. Regularly replacing crimping dies and seals ensures optimal hydraulic hose installation performance.
8.3 Troubleshooting and Fixing Common Problems
Address common problems such as inconsistent crimps, pressure issues, or mechanical failure by performing diagnostic checks and making necessary repairs. Regular hydraulic tool maintenance is key to extending the life of your hydraulic crimping machine.
9. Innovations in Hydraulic Hose Crimping Technology
Hydraulic hose crimping technology has come a long way, with new developments aimed at improving speed, accuracy, and ease of use.
9.1 Latest Advancements in Crimping Machines
Recent innovations include fully automated hydraulic crimping machines, which enhance precision and reduce the need for manual intervention. These machines offer greater control over the crimping process, ensuring consistency across high-volume applications.
9.2 The Future of Crimping Technology
The future of crimping equipment looks exciting, with advancements in artificial intelligence and machine learning expected to revolutionize the way crimping machines are calibrated, operated, and maintained.
10. Understanding Crimping Standards and Certifications
Industry standards and certifications ensure that hydraulic hose crimpers meet safety, performance, and quality benchmarks. These standards protect businesses from subpar equipment that could result in failures or accidents.
10.1 Industry Standards for Hydraulic Crimping
Common standards include ISO 9001 for quality management systems and SAE J517, which sets guidelines for hydraulic hose assemblies. These certifications ensure that crimping machines for hoses meet specific safety and quality requirements.
10.2 How to Ensure Your Crimper Meets Required Certifications
Before purchasing a crimper, ensure that the machine is certified by recognized bodies. This guarantees that the equipment meets hydraulic hose standards for safety, performance, and reliability.
11. Choosing the Right Hydraulic Hose Crimper for Your Business
Selecting the right hydraulic hose crimper can greatly impact the efficiency of your operations. Here’s a guide to help you make the best choice for your business needs.
11.1 Key Considerations for Sourcing Crimpers
When choosing a crimper, consider factors like hose fitting connection, hydraulic hose specifications, and the crimper’s capacity. Make sure the machine is compatible with the materials and pressure levels you’ll be working with.
11.2 How to Evaluate Suppliers and Manufacturers
Look for reputable suppliers who offer high-quality, certified industrial hydraulic crimpers. Check reviews and ask for demonstrations to ensure that the machine meets your needs.
11.3 Making the Best Investment for Your Company
Investing in a high-quality hydraulic hose crimper can pay off in the long run by reducing the risk of failures and improving productivity.
12. Cost of Hydraulic Hose Crimpers
The cost of hydraulic hose crimpers varies widely based on factors such as size, features, and power source. Let’s explore how to assess the total cost of ownership.
12.1 Factors That Affect the Price of Crimpers
Key factors include the crimper’s capacity, the materials used, and the features it offers, such as automation or portability.
12.2 How to Get the Best Value for Your Investment
While cheaper models may seem appealing, consider the long-term benefits of investing in a durable, high-performance crimper to avoid frequent repairs or replacements.
13. Common Mistakes When Using Hydraulic Hose Crimpers
Even experienced operators can make mistakes that affect the quality of their crimps. Here are some common pitfalls to avoid.
13.1 Over-crimping vs Under-crimping
Finding the right balance of pressure is crucial. Over-crimping can damage hoses, while under-crimping may lead to leaks.
13.2 Ignoring Manufacturer Specifications
Always follow the manufacturer’s guidelines for crimping settings and hose sizes. Ignoring these instructions can lead to suboptimal crimps and increased failure rates.
13.3 Using the Wrong Fitting
Ensure that the hydraulic fitting is compatible with the crimper and the hose material. Using incompatible fittings can compromise the seal and cause leaks.
14. Frequently Asked Questions About Hydraulic Hose Crimpers
14.1 What is the Difference Between Crimping and Clamping?
While both methods involve attaching a fitting to a hose, crimping involves permanently deforming the hose to create a seal, while clamping simply secures the fitting in place.
14.2 How Often Should a Hydraulic Hose Crimper be Calibrated?
It’s recommended to calibrate your crimper regularly, typically every 6 to 12 months, depending on usage.
14.3 Can Hydraulic Hose Crimpers be Used for All Types of Hoses?
Hydraulic hose crimpers are designed for specific hose types. Always check the crimper’s specifications to ensure compatibility with your hoses.
15. Conclusion
15.1 Final Thoughts on the Importance of Hydraulic Hose Crimpers
Hydraulic hose crimpers are essential to the success of any business that relies on hydraulic systems. These tools ensure safety, reliability, and efficiency, preventing costly failures and maintaining the integrity of your operations.
15.2 How Choosing the Right Crimper Can Boost Efficiency and Safety
Selecting the right hydraulic crimper not only improves the longevity of your equipment but also helps avoid downtime, accidents, and costly repairs. With the right machine, you’ll boost your business’s productivity and maintain seamless operations for years to come.